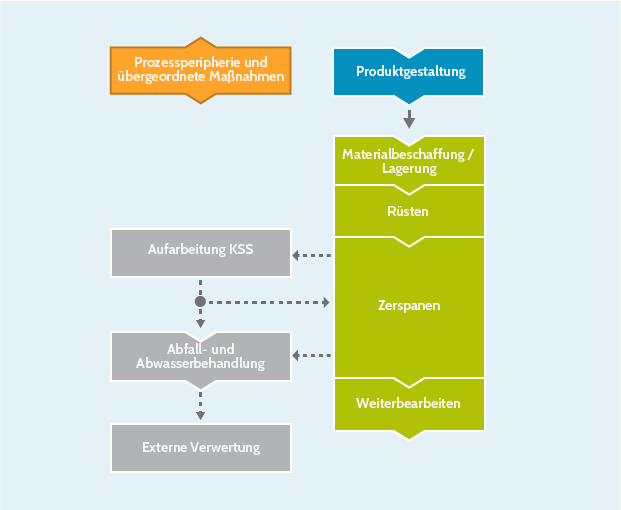
Produktgestaltung
Beste verfügbare Technik
Digital Prototyping
- der Einsatz von Digital Prototyping unterstützt eine nachhaltige Produktentwicklung
- liefert Materialeigenschaften wie Kosten, CO2-Belastung, Wasserverbrauch, Energieverbrauch, RoHS-Compliance, Recyclingfähigkeit etc.
Einbeziehen der Produktentwicklung
- bereits bei der Produktentwicklung sollten Überlegungen einbezogen werden, wie Schleifprozesse vermieden werden können: z.B. durch Konstruktionsänderungen, gebaute Komponenten, andere Formgebungsverfahren wie Pulvermetallurgie und Eindruckguss
Quelle(n):
- Informationszentrum für betrieblichen Umweltschutz [IBU] (2012): Betrieblicher Umweltschutz [online]. Ministerium für Umwelt, Klima und Energiewirtschaft Baden-Württemberg, verfügbar unter: Link
Reduzieren der Aufmaße
- Möglichst endabmessungsnahe Halbzeuge und Werkstücke reduzieren nicht nur die Abfallmenge, sondern auch den Materialeinsatz und den Fertigungsaufwand. Bei Einzelteilfertigung bzw. kleinen Stückzahlen ist dies jedoch nicht immer realisierbar.
Quelle(n):
- Informationszentrum für betrieblichen Umweltschutz [IBU] (2012): Betrieblicher Umweltschutz [online]. Ministerium für Umwelt, Klima und Energiewirtschaft Baden-Württemberg, verfügbar unter: Link
Projekte
Ecobiente – Nachhaltige Güter erfolgreicher gestalten
- Das Projekt Ecobiente behandelt am Beispiel des Bedarfsfeldes Bauen und Wohnen die Möglichkeiten, nachhaltige Güter attraktiver und zielgruppengerechter zu konzipieren und zu vermarkten. Es richtete sich vor allem an Unternehmen und GestalterInnen, die ökologisch nachhaltige Güter entwickeln bzw. anbieten.
Materialbeschaffung / Lagerung
Beste verfügbare Technik
Betrachtung der gesamten Fertigungskette
- Die Betrachtung der Fertigungskette, in die das jeweilige Bearbeitungsverfahren eingebunden ist, ist hinsichtlich der Effizienzsteigerung von erheblicher Bedeutung. Einflüsse aus vorgeschalteten Bearbeitungsprozessen sind ebenso zu berücksichtigen wie die Auswirkungen der verwendeten Bearbeitungs- u. Hilfsstoffe auf die Folgeprozesse.
- Eine ganzheitliche Prozessbetrachtung zeigt Zusammenhänge in der Produktion auf und eröffnet ein großes Potenzial zur Prozessoptimierung, sowohl in ökologischer als auch in ökonomischer Hinsicht.
Beispiele:
- Auf Halbzeugen oder Vorprodukten aufgetragene Korrosionsschutzmittel können negative Einflüsse auf die Wirkung von Kühlschmierstoffen und damit die Bearbeitungsqualität haben und zu kurzen Badstandzeiten, zusätzlichen Hautbelastungen bei den Mitarbeitern und zu einem erhöhtem Abfallaufkommen führen.
- Die eingesetzten Kühlschmierstoffe werden über die Werkstücke aus dem Prozess ausgetragen und haben damit wiederum erhebliche Auswirkungen auf den Folgeprozess, sei es ein Reinigungsprozess oder ein weiterer Prozess zur Oberflächenbehandlung.
Quelle(n):
- Informationszentrum für betrieblichen Umweltschutz [IBU] (2012): Betrieblicher Umweltschutz [online]. Ministerium für Umwelt, Klima und Energiewirtschaft Baden-Württemberg, verfügbar unter: Link
Gemeinsame Lösungen für IT und Industrie
- gemeinsame modulare Basis verringert die Lagerhaltung, vereinfacht die Bereitstellung und senkt die Kosten
- hinzu kommen Skalierbarkeit und Investitionssicherheit
Hilfsstoffbedingte Abfälle reduzieren
Maßnahmen zur Reduzierung von Umweltrisiken und hilfsstoffbedingte Abfällen:
- Vorratsgebinde für Öle, Kühlschmierstoffe usw. sollten immer über Auffangwannen gelagert werden, auch um Tropfverluste zuverlässig aufzufangen.
- Jedes Gebinde eindeutig kennzeichnen.
- Die Anzahl der eingesetzten Produkte sollte so gering wie möglich gehalten werden.
- Die Austragsverluste sollten möglichst gering gehalten werden.
Quelle(n):
- Informationszentrum für betrieblichen Umweltschutz [IBU] (2012): Betrieblicher Umweltschutz [online]. Ministerium für Umwelt, Klima und Energiewirtschaft Baden-Württemberg, verfügbar unter: Link
Videos
Perfekter Materialstrom im Schwarzwald
Mit dem Aufruf des Videos erklären Sie sich einverstanden, dass Ihre Daten an YouTube übermittelt werden und dass Sie die Datenschutzerklärung gelesen haben.
Rüsten
Beste verfügbare Technik
Auswahl der Schneidstoffsorten und Geomtrien
- die richtige Auswahl der Schneidstoffsorten und Geomtrien kann zu einer Leistungssteigerung hinsichtlich der Standzeiten, der Produktivität und der Prozesssicherheit und somit zur Effizienzsteigerung führen
- innovative Schneidstoffe führen zu Verschleißreduzierung und somit zu Einsparungen im Werkzeugverbrauch
- neben dem Effekt der Verschleißreduzierung wirkt sich die Leistung der Zerspanungswerkzeuge auch positiv auf die Maschinenkosten, die Maschineneinstellkosten und die Werkzeugwechselkosten aus: höhere Schnittparameter verbessern die Produktivität; eine höhere Maßhaltigkeit reduziert die Maschineneinstellkosten, da weniger Ein -u. Nachstellungen notwendig sind.
- eine FEM-Simulation bietet die Möglichkeit das Einsatz- und Verschleißverhalten vorherzusagen: Dieses wird werkzeugseitig durch die Geometrie, den Substratwerkstoff und das Schichtsystem beeinflusst.
- Durch verbesserte Werkzeugtechnologien (Beschichtungen, verbesserte Oberflächen) können die traditionellen Aufgaben des Kühlschmierstoffs (Schmieren, Kühlen, Spänetransport) inzwischen auch mit diesen Technologien bewältigt werden und somit kann ggf. auf den Einsatz von KSS verzichtet werden.
Effiziente Werkzeugvoreinstellung
Der Einsatz von Werkzeugvoreinstellgeräten zum Vermessen von Dreh- und Fräswerkzeugen befreit die Werkzeugmaschinen von unnötigen Rüstzeiten und steigert somit ihre Verfügbarkeit.
Hydrostatisches Führungssystem
Der Einsatz eines hydrostatischen Führungssystems ermöglich
- Positioniergenauigkeit
- Prozesssicherheit
und somit weniger Ausschuss.
Messtaster in Bearbeitungszentren
- durch den Einsatz von Messtasters in Bearbeitungszentren kann kostenintensiver Ausschuss vermeiden werden
Präzisionsspannfutter
der optimierte Einsatz von Präzisionsspannfutter
- reduziert die Werkzeugkosten (um ca. 10%)
- erhöht Leistung
- erhöht Qualität und senkt somit den Aussschuß
Rüstkosten senken mit Nullpunktspannsystemen
- durch den Einsatz eines Nullpunktspannsystems lässt dich das Rüsten, Messen, Ausrichten und Spannen einfacher gestalten
- die Maschinenauslastung wird erhöht
- die Amortisationszeit für ein Nullpunktspannsystem liegt zwischen 6 - 18 Monaten (abhängig von der Anzahl der täglichen Vorrichtungswechsel)
Stabilisierung des Werkstücks durch Niederhalter
- Mit einem Niederhaltersystem findet eine zusätzliche Stabilisierung des Werkstücks direkt an der Frässtelle statt.
- Das Frässtück (insbesondere kleine Frässtücke) wird so sicher gehalten und ein "Ausfransen" an seiner Oberfläche vermieden.
Werkzeugauswahlsystem
- durch die Auswahl der geeigenten Werkzeuge oder Wendeschneidplatten wird die wirtschaftlichste Lösung für eine konkrete Aufgabenstellung des Anwenders ermittelt
- der Nutzer bekommt eine Empfehlung für die Bearbeitungsstrategie und Kosten je Bearbeitungsoperation
- individuelle Ergebnisse der Standzeiten und Schnittdaten lassen sich ebenfalls darstellen
Werkzeugschleifen
- durch das Rekonditioning (Wiederbeschichten und Nachschleifen von Werkzeugen) werden Werkzeugkosten gesenkt, Ressourcen geschont und Abfall vermindert
- dabei spielen effiziente Spannmittel zum automatisierten Werkzeugschleifen eine wichtige Rolle, denn eine exzellente Form- und Maßhaltigkeit an der Werkzeugschneide erhöht die Standzeit der Werkzeuge wesentlich
- mithilfe spezieller Verschleißbilder und Verschleißgrenzen geben wichitge Hinweise, wie sie die Werkzeuge produktiver einsetzen können und Gegenmaßnahmen können identifiziert werden
Zerspanen
Beste verfügbare Technik
Abfallvermeidung durch Vermeidung von Nassbearbeitung
- insbesondere bei Neuinvestitionen sollten die Möglichkeiten der Trockenbearbeitung/MMS geprüft werden
- somit können neben unbrauchbar gewordenen KSS weitere KSS-bedingte Abfälle aus der spanenden Metallbearbeitung vermieden werden:
- Ölhaltige Schleif, Hon- u. Läppschlämme
- KSS-getränkte Filtermittel (Filtervliese, Filterpatronen)
- Ölbindemittel (Aufsaugmittel für verspritzte, verschüttete KSS)
- KSS-verunreinigte Putztücher und Arbeitskleidung
- Verölte Späne (insbesondere beim Einsatz nichtwassermischbarer KSS)
- Nicht zuletzt sind natürlich auch die bearbeiteten Werkstücke beim Verlassen der Maschine mit KSS behaftet (lässt sich durch Abtropfen, Schleudern usw. reduzieren) und müssen meist vor der Weiterverarbeitung gereinigt werden, mit entsprechenden Umweltbelastungen des eingesetzten Reinigungsverfahrens.
Quelle(n):
- Informationszentrum für betrieblichen Umweltschutz [IBU] (2012): Betrieblicher Umweltschutz [online]. Ministerium für Umwelt, Klima und Energiewirtschaft Baden-Württemberg, verfügbar unter: Link
Abfallvermeidung und Umweltentlastung bei der Nassbearbeitung (KSS)
Maßnahmen zur Umweltentlastung und Abfallvermeidung durch die bei der Nassbearbeitung verwendeten KSS:
- Durch regelmäßiges Umwälzen oder Belüften sowie durch Entfernung von Fremdölen und anderen Verunreinigungen lassen sich die Standzeiten von KSS-Emulsionen auch bei einzelversorgten Maschinen auf 3-6 Monate erhöhen. Zudem wird die Arbeitshygiene deutlich verbessert.
- Der Eintrag von Verschmutzungen (Fremdöle, Fremdstoffe) durch die Maschine, die zu bearbeitenden Werkstücke und die Mitarbeiter sollte vermieden werden. Einfache Messungen (pH-Wert mit pH-Papier, Konzentration mit Hand-Refraktometer, Leitwert, Geruch und optischer Beurteilung) geben schnell Hinweise, ob der Kühlschmierstoff sich verändert hat und noch gegensteuert werden kann.
- Bereits bei der Auswahl sollte auf möglichst umweltgerechte und humanverträgliche Inhaltsstoffe des KSS geachtet werden.
- KSS erfordern Sicherungsmaßnahmen zum Gewässerschutz, sowohl bei der Lagerung, als auch beim Einsatz.
- Durch den Bearbeitungsprozess und über Fremdeinträge (Werkstücke, Luft, Mitarbeiter) gelangen weitere Schadstoffe in den KSS und führen insbesondere bei wassergemischten Systemen zu zusätzlichen Belastungen (z.B. Verkeimung). Bei wassergemischten KSS ist die Bildung von Nitrosaminen (krebserzeugend) zu vermeiden, dabei sind die Vorgaben der Technischen Regel für Gefahrstoffe (TRGS) 611 zu beachten.
- Bei KSS-Ölen spielt der Brandschutz bei der Lagerung und insbesondere auch beim Einsatz in der Bearbeitungsmaschine eine bedeutende Rolle. Beim Betrieb der Bearbeitungsmaschinen ist neben dem Brandschutz auch der Explosionsschutz besonders zu berücksichtigen. Durch die starken Verwirbelungen in der Werkzeugmaschine und der hohen thermischen Belastung an der Bearbeitungsstelle bilden sich KSS-Nebel u. -Dämpfe, so dass maschinenseitig Einrichtungen zum Brand- u. Explosionsschutz vorhanden sein müssen. Bei neuen Maschinen muss der Bearbeitungsraum gekapselt sein.
- Auf hautschädigende KSS-Komponenten verzichten, Hautschutzpläne erstellen und Mitarbeiter informieren (Arbeitsschutz).
- Beim Einsatz nichtwassermischbarer KSS (KKS-Öle) ist darauf zu achten, dass die Verschleppungsverluste über Späne und Werkstücke möglichst gering gehalten werden. Abtropfzonen und gegebenenfalls Späneschleudern sind wirkungsvolle Gegenmaßnahmen. Abgetrennte Öle können problemlos wieder in den KSS-Kreislauf zurückgeführt werden.
- Zu entsorgende KSS sind generell als gefährlicher Abfall (Sonderabfall) eingestuft. Während nichtwassermischbare KSS sehr lange Standzeiten aufweisen (oft "Lebensdauerfüllung") sind die wassergemischten KSS-Systeme wesentlich empfindlicher. Um vorzeitige Verkeimung zu vermeiden und lange Badstandzeiten zu erzielen, ist eine regelmäßige Überwachung und Badpflege notwendig. In einzelversorgten Maschinen gelten Badstandzeiten von 1/2 Jahr und in Zentralanlagen von mind. 2 Jahren als Anhaltswerte.
- Eine Umstellung auf Trockenbearbeitung bzw. Minimalmengen-Schmierung (MMS) kann vorteilhaft sein und sollte bei Neuinvestitionen auf jeden Fall in Betracht gezogen werden. Gerade, wenn manche Werkzeugmaschinen nur sporadisch benutzt werden, ist die Bearbeitung mit MMS sehr vorteilhaft, da insbesondere Kühlschmierstoff-Emulsionen in Stillstandszeiten schnell verkeimen. Dauernd wechselnde Bearbeitungsprozesse erfordern dafür jedoch Erfahrung und Engagement.
Quelle(n):
- Informationszentrum für betrieblichen Umweltschutz [IBU] (2012): Betrieblicher Umweltschutz [online]. Ministerium für Umwelt, Klima und Energiewirtschaft Baden-Württemberg, verfügbar unter: Link
Auswuchtsystem sichert Qualität in der High-Speed-Fertigung
- erhöhte Werkzeug- und Spindelstandzeiten
- hohe und sichere Qualität der Bauteile
Effiziente Werkzeugmaschinen
- wettbewerbsfähigkeit im Werkzeugmaschinenbau spiegelt sich nicht nur im Anschaffungspreis, der Maschine, sondern auch in den Verbrauchswerten über den gesamten Lebenszyklus wider
- ganzheitliche Sichtweisen führen zu Energieeinsparungen von 40%
Maßnahmen sind zum Beispiel:
- Frequenzumwandlung an Pumpen (reduzieren die Grundlast der Maschine), Funktionell hochwertige Dichtungen und Abwärmenutzung
- funktionell hochwertige Dichtungen
- Abwärmenutzung
- die volle Auslastung der Maschine erhöht die Effizienz
- Zweispindler statt Einspindler
- Hydraulikfreie Maschinen
- die volle Auslastung der Maschinen sichert zumeist die höchste Effizienz
- kryogene Minimalmengenschmiersysteme zur gezielten Schneidenkühlung mittels flüssigem Stickstoff führen zu längeren Werkzeugstandzeiten
- Nadeldüsen im Schleifprozess sorgen für einen konzentrierten, zielgerichtetn Schleifmittelstrahl. Dadurch werde Durchflussmenge, Pumpendruck, Kühlmittelverdunstung und letztlich Energieverbrauch sowie Umweltentlastung reduziert
Bewertung von Energieeffizienz:
- Ermittlung der Leistung für definierte Betriebszustände, Bewertung von Testwerkstücken zur Energiemessung und Kriterienkatalog mit Maßnahmen zur Verbesserung der Energieeffizienz mit dem Ziel den Energieverbruach der Werkzeugmaschine um 30% zu senken
Es wird an der thermo-energetischen Gestaltung von Werkzeugmaschinen geforscht.
Energieeffiziente Zerspanung
- Optimierung der Spanungsquerschnittsform senkt Energiebedarf
- Ein großer Teil des Energiebedarfs einer spanenden Werkzeugmaschine wird für den Antrieb der Hauptspindel und für den Zerspanprozess selbst benötigt. Durch die Spanungsquerschnittsform, welche sich aus der Werkzeuggeometrie, dem Vorschub und der Schnitttiefe ergibt, lässt sich die zur Zerspanung eines bestimmten Werkstückvolumens erforderliche Energie beeinflussen.
- Somit kann der Energiebedarf für den Zerspanprozess verringert bzw. die Produktivität bei vorgegebener Spindelauslastung erhöht werden.
Fräsen von CFK
- Kohlenstofffaserverstärkte Kunststoffe (CFK) neigen zu Absplitterungen und Ausbrüchen
- die Gestaltung optimierter Werkzeuggeometrien und die Entwicklung angepasster Bearbeitungsstrategien sind notwendig um Absplittern zu vermeiden und somit Ausschuss und Reparaturaufwand zu reduzieren
KSS-Versorgung der Werkzeugmaschinen optimieren
- Die Versorgung der Bearbeitungsstelle mit Kühlschmierstoffen (KSS) erfolgt entweder über ein in der Werkzeugmaschine enthaltenes System (Einzelversorgung) oder über eine zentrale Versorgungseinheit, die mehrere Maschinen bedient (Zentralanlage). Bei beiden Systemen werden die KSS im Kreislauf geführt. Hauptaufgaben der KSS-Versorgung sind
- die zuverlässige Bereitstellung von KSS an den Bearbeitungsstellen
- den Erhalt der KSS im gebrauchsfähigen Zustand (Badpflege)
- Die Konzeption der Versorgungsanlagen richtet sich daher nach dem verwendeten KSS, dem Bearbeitungsverfahren und den zu bearbeiteten Werkstoffen. Für die Entscheidung, ob eine Einzel oder Zentralversorgung besser ist, sind neben Wirtschaftlichkeitsbetrachtungen auch die räumlichen Verhältnisse (Standorte der Maschinen, Möglichkeiten der Leitungsverlegung) und die erforderliche Flexibilität (Maschinenverlagerungen) maßgebend.
- Auch bei der KSS-Versorgung gilt der Grundsatz: Nur so viel wie nötig. "Sicherheitshalber" eingesetzte große KSS-Mengen bedingen unnötige Kosten.
- Energietipp: Pumpen nicht gegen gedrosselte Ventile laufen lassen. Die Bedarfsregelung über drehzahlgesteuerte Pumpen spart Energie.
Quelle(n):
- Informationszentrum für betrieblichen Umweltschutz [IBU] (2012): Betrieblicher Umweltschutz [online]. Ministerium für Umwelt, Klima und Energiewirtschaft Baden-Württemberg, verfügbar unter: Link
Leistungssteigerung von Zerspanwerkzeugen
- Schneidkantenpräparation gezielt einsetzen: neben der Analyse des Einsatzverhaltens für die Dreh- und Fräsbearbeitung ist insbesondere die gezielte und prozesssichere Herstellung der Kantengeometrie von großer Bedeutung
- die Leistungsfähigkeit von Zerspanungswerkzeugen lässt sich durch eine gezielte Schneidkantenpräparation erhöhen: Die Standzeit nimmt bei statischen sowie dynamischen thermomechanischen Belastungskollektiv signifikant zu
- die Ermittlung der für die jeweilige Anwendung geeigneten Schneidkatengeometrie wird durch Standzeitkarten ermöglicht; diese Karten können für beliebige Werkzeuge sowie Werkstoffe anhand von Versuchen erstellt werden
- des Weiteren bieten präparierte Werkzeuge eine höhere Prozesssicherheit, da ein sporadisches Werkzeugversagen verhindert und somit eine engere Toleranz der Prozesshauptzeiten möglich wird
Maschinenraumsimulationen
- Maschinenraumsimulationen bieten die Möglichkeit Prozesse bei NC-Maschinen zu optimieren
- Vermeiden von Maschinenstillständen bzw. Produktivitätseinbußen
Maßnahmen zur Vermeidung und Verwertung von Schleifschlämmen
Maßnahmen zur Vermeidung und Verwertung von Schleifschlämmen:
- Bereits bei der KSS-Auswahl sollte auf möglichst umweltgerechte und humanverträgliche Inhaltsstoffe geachtet werden.
- Bei Schleifmaschinen ist neben dem Brandschutz der Explosionsschutz besonders zu berücksichtigen. Durch die starke Verwirbelung in der Werkzeugmaschine und der hohen thermischen Belastung an der Bearbeitungsstelle bilden sich KSS-Nebel u. -Dämpfe, so dass maschinenseitig Einrichtungen zum Brand- u. Explosionsschutz vorhanden sein müssen. Bei neuen Maschinen muss der Bearbeitungsraum generell gekapselt sein. Bei offenen Maschinen sollte eine wirksame Absaugung installiert sein.
- Abfallvermeidung: Insbesondere beim Einsatz von KSS-Ölen ist darauf zu achten, dass die Verschleppungsverluste über Werkstücke und insbesondere über die Schleifschlämme möglichst gering gehalten werden. Abtropfzonen und gegebenenfalls Schlammpressen sind wirkungsvolle Maßnahmen. Abgetrennte Öle können problemlos wieder in den KSS-Kreislauf zurückgeführt werden.
- KSS werden entweder in der Maschine (Einzelversorgung) oder über zentrale Versorgungsanlagen im Kreislauf geführt. Die teilweise großen Mengen wassergefährdender Stoffe bedingen Sicherungsmaßnahmen zum Gewässerschutz, sowohl bei der Lagerung, als auch beim Einsatz.
- Durch den Bearbeitungsprozess und über Fremdeinträge (Werkstücke, Luft, Mitarbeiter) gelangen weitere Schadstoffe in den KSS und führen insbesondere bei wassergemischten Systemen zu zusätzlichen Belastungen (z. B. Verkeimung). Zur Vermeidung der möglichen Bildung von Nitrosaminen (krebserzeugend) bei wassergemischten KSS sind die Vorgaben der Technischen Regel für Gefahrstoff (TRGS) 611 zu beachten.
- Auf hautschädigende KSS-Komponenten verzichten, Hautschutzpläne erstellen und Mitarbeiter informieren (Arbeitsschutz).
- Während nichtwassermischbare KSS sehr lange Standzeiten aufweisen (oft "Lebensdauerfüllung") sind die wassergemischten KSS-Systeme wesentlich empfindlicher. Um vorzeitige Verkeimung zu vermeiden und um lange Badstandzeiten zu erzielen, ist eine regelmäßige Überwachung und Badpflege notwendig. In einzelversorgten Maschinen gelten Badstandzeiten von 1/2 Jahr und in Zentralanlagen von mindestens 2 Jahren als Anhaltswerte.
- Schleifschlämme können Ölgehalte von bis zu 60 % und darüber aufweisen. Verfahren zur Abtrennung des Ölanteils rentieren sich daher schon bei Anfallmengen von 10 t/a. Außerdem verbessert ein geringerer Ölgehalt die Verwertungsmöglichkeiten.
Quelle(n):
- Informationszentrum für betrieblichen Umweltschutz [IBU] (2012): Betrieblicher Umweltschutz [online]. Ministerium für Umwelt, Klima und Energiewirtschaft Baden-Württemberg, verfügbar unter: Link
Minimalmengen-Schmierung (MMS)
- Bei vielen Bearbeitungsoperationen werden mit reiner Trockenbearbeitung in der Praxis nur unzureichende Bearbeitungsergebnisse erreicht, obwohl bei Vorversuchen gute Ergebnisse erzielt wurden. Hier besteht mit dem Einsatz der MMS zur Erhöhung der Prozesssicherheit eine kostengünstige, sichere und universell einsetzbare Ergänzungsmöglichkeit zur Trockenbearbeitung.
- Bei der MMS wird der Wirkbereich der Werkzeugschneiden oder das Werkzeug selbst mit kleinsten Mengen Öl bzw. MMS-Medium benetzt, um den notwendigen Schmiereffekt zur Reduzierung der Reibung zwischen Span und Spanfläche des Werkzeugs zu erreichen. Unter Verwendung geeigneter Schmierstoffe haben die Erfahrungen gezeigt, dass in der Regel Mengen im Bereich von 10 - 20 ml/h zur Erzielung der gewünschten Schmierwirkung ausreichen. Bei kleinen Werkzeugen sind auch Anwendungen mit ca. 2 ml/h bekannt. Eine Kühlwirkung kann mit dem MMS-Einsatz kaum erzielt werden.
- In Ergänzung zur reinen Trockenbearbeitung eignen sich zur Anwendung der MMS insbesondere
- Bearbeitungsverfahren mit geometrisch bestimmter Schneide (Fräsen, Bohren, Sägen usw.)
- Bearbeitungsverfahren, bei denen die Kühlfunktion nicht im Vordergrund steht
- Prozesse, bei denen der Eingriffsbereich des Werkzeugs gut mit Schmierstoff benetzt werden kann.
Zur Applikation der geringen Schmierstoffmengen auf den Zerspanungsbereich werden im Wesentlichen 3 Typen von MMS-Auftragssystemen eingesetzt:
- Überdruck-Sprühsysteme: Der Schmierstoffbehälter steht unter Druck (Pressluft), die Mengendosierung erfolgt über Drosselventile oder Kapillaren.
- Drucklose Sprühsysteme: Die Schmierstoffmenge wird aus einem drucklosen Behälter über Dosierpumpen gefördert.
- Airless-Auftragssysteme ("Spucksysteme"): Hierbei werden kleinste Schmierstofftropfen ohne Luftstrahl per Impuls auf die Bearbeitungsstelle "geschossen".
- Grundsätzlich lässt sich beim MMS-Einsatz zwischen äußerer Zuführung (durch Düsen von außen auf die Bearbeitungsstelle) und innerer Zuführung (durch die Spindel und das Werkzeug) des Öl-Luft-Gemisches unterscheiden. Von entscheidender Bedeutung für die Wirksamkeit der MMS ist die Applikationstechnik in der Werkzeugmaschine. Diese muss an die spezifischen Randbedingungen des Produktionsprozesses angepasst werden, um die Zerspanstelle möglichst zielgenau mit den geringen Schmierstoffmengen zu versorgen.
- Typische Einsatzbeispiele der äußeren MMS-Zuführung sind Säge- u. Fräsprozesse. Hier ist die Zugänglichkeit von außen in der Regel gut und die Schnitttiefen gering, so dass eine ausreichende Benetzung des Werkzeugs jederzeit gewährleistet ist. Auch Drehbearbeitungen, insbesondere im Werkstattbereich, lassen sich gut per äußerer Zuführung realisieren. MMS-Systeme mit äußerer Zuführung lassen sich in der Regel bei bestehenden Maschinen einfach nachrüsten.
- Systeme mit innerer Zuführung werden bevorzugt bei Bohr- u. Reiboperationen eingesetzt, da bei großen Bohrtiefe/Durchmesser-Verhältnissen (l/d > 3) eine MMS-Versorgung von außen nicht mehr sichergestellt werden kann. Bei der inneren Zufuhr des MMS-Mediums muss das Öl/Luft-Gemisch weit vor der Austrittsstelle erzeugt werden. Bei zu großen Öltröpfchen sowie bei ungeeigneten Strömungskanälen besteht die Gefahr, dass sich das Gemisch auf dem Weg zur Austrittsstelle wieder entmischt (insb. bei hohen Drehzahlen aufgrund der Fliehkräfte), sich Ablagerungen bilden und große Tröpfchen unregelmäßig austreten. Gleichmäßige Bearbeitungsergebnisse und Prozesssicherheit sind damit nicht mehr gewährleistet. Für die innere Zuführung sind daher MMS-Systeme, die sehr feine Tröpfchen erzeugen besser geeignet. Die Werkzeugmaschine benötigt im Falle einer inneren Zuführung eine spezielle Spindel, durch die der Schmierstoff an das Werkzeug geleitet werden kann. Insbesondere bei den heute üblichen hohen
Spindeldrehzahlen werden an die benötigten Drehdurchführungen hohe Anforderungen gestellt.
- Für die diskontinuierliche Beaufschlagung, z.B. bei Stanz- u. Biegeprozessen oder für die Herstellung kleiner Gewinde eignen sich auch so genannte Airless-Auftragssysteme, bei denen kleinste Tropfen auf die Bearbeitungsstelle "gespuckt" werden.
Quelle(n):
- Informationszentrum für betrieblichen Umweltschutz [IBU] (2012): Betrieblicher Umweltschutz [online]. Ministerium für Umwelt, Klima und Energiewirtschaft Baden-Württemberg, verfügbar unter: Link
Ölfreier Schmierstoff
Deutscher Rohstoffeffizienz-Preis 2011 für die Entwicklung eines ölfreien Schmierstoffs auf Polymerbasis zum Einsatz in der Metallverarbeitung: der neue Schmierstoff kann die bisher auf Mineralölbasis bestehenden Schmierstoffe in der spanenden Fertigung ersetzen
Vorteile:
- deutliche geringere Umweltwirklung
- vermindert Werkzeugverschließ und verlängert Werkzeugstandzeit
- die geschmierten Teile lassen sich einfacher reinigen
- erhöht die Arbeitssicherheit und -hygiene, da sich kein Ölnebel bildet und weniger Biozide zugegeben werden müssen
Reduzierung von KSS (Schleifen)
- Spritz- u. Austragsverluste gering halten
- zur Reduzierung der Austragsverluste über die Schleifschlämme bieten sich hilfsmittelfreie Filterverfahren wie Magnetwalzen oder Umlaufbandfilter an
- Entsorgungshinweise: Ölhaltige Schleifschlämme dürfen nicht den Spänen zugefügt, sondern müssen separat als gefährlicher Abfall entsorgt werden. Für ölhaltige Schleifschlämme bestehen verschiedene Verwertungsmöglichkeiten, die für Handwerksbetriebe wegen der meist kleinen Mengen allerdings nur beschränkt zugänglich sind. Hartmetallschlämme sollten separat erfasst werden, da siegut verwertbar sind und auch in kleinen Mengen hoch vergütet werden.
Quelle(n):
- Informationszentrum für betrieblichen Umweltschutz [IBU] (2012): Betrieblicher Umweltschutz [online]. Ministerium für Umwelt, Klima und Energiewirtschaft Baden-Württemberg, verfügbar unter: Link
RFID für Toolmanagement
- Werkzeugverwaltung via Tool-Tag mit RFID reduziert den Papieraufwand in der Produktion
- vereinfachte Nachverfolgbarkeit, Verschleiß-Informationen, Steuerung der Wiederaufbereitung, Beschaffung von Verschleißkomponenten
Softwareunterstützung / Simulation von Probeläufen
Vorteile von Softwareunterstützung / Simulation von Probeläufen:
- Simulation sichert Präzision
- Vermeiden von kostenspieligen und gefährlichen Irrtümern
- Test- und Einfahrzeiten verkürzen
- Bearbeitungsprozess verkürzen (15%-30%) durch höhere Abtragsleistungen
- Werkzeugstandzeiten verlängern
- Maschinenkollisionen vermeiden
- Bearbeitungsabläufe und Schnittdaten optimieren
- Optimierung der Bearbeitungsvorschübe des NC-Programms, sodass die Fertigung effizienter und schonende abläuft
- Ausfallrate senken
- Effizienz und Maschinenpark bei der Auswahl berücksichtigen
- hohe Bearbeitungsqualitäten
Spanleitgeometrien für langspanende Aluminium- und Magnesiumlegierungen
- verbesserte Produktivität
- enge Toleranzen
- reduzierter Energieverbrauch
Stromqualität messen
- durch Stromschwankungen verursachte Qualitätsmängel vermeiden
Umweltentlastung beim Gewindeschneiden und Räumen (KSS)
Maßnahmen zur Umweltentlastung und Abfallvermeidung durch die beim Gewindeschneiden und Räumen verwendeten KSS-Öle:
- Bereits bei der KSS-Auswahl sollte auf möglichst umweltgerechte und humanverträgliche Inhaltsstoffe geachtet werden.
- Bei KSS-Ölen spielt der Brandschutz beim Lagern und insbesondere auch beim Einsatz in der Bearbeitungsmaschine eine bedeutende Rolle.
- Kühlschmierstoffe werden entweder in der Maschine (Einzelversorgung) oder über zentrale Versorgungsanlagen im Kreislauf geführt. Die teilweise großen Mengen wassergefährdender Stoffe bedingen Sicherungsmaßnahmen zum Gewässerschutz, sowohl bei der Lagerung, als auch beim Einsatz.
- Beim Betrieb der Bearbeitungsmaschinen ist neben dem Brandschutz auch der Explosionsschutz besonders zu berücksichtigen. Insbesondere durch die hohe thermische Belastung an der Bearbeitungsstelle bilden sich KSS-Nebel u. -Dämpfe, sodass maschinenseitig Einrichtungen zum Brand- u. Explosionsschutz vorhanden sein müssen. Bei neuen Maschinen muss der Bearbeitungsraum generell gekapselt sein.
- Auf hautschädigende KSS-Komponenten verzichten, Hautschutzpläne erstellen und Mitarbeiter zu informieren (Arbeitsschutz).
- Beim Einsatz nichtwassermischbarer KSS (KKS-Öle) ist darauf zu achten, dass die Verschleppungsverluste über Späne und Werkstücke möglichst gering sind. Abtropfzonen und gegebenenfalls Späneschleudern sind wirkungsvolle Gegenmaßnahmen. Abgetrennte Öle können problemlos wieder in den KSS-Kreislauf zurückgeführt werden.
- Zu entsorgende KSS sind generell als Sonderabfall eingestuft. Nichtwassermischbare KSS weisen jedoch in der Regel sehr lange Standzeiten auf (oft "Lebensdauerfüllung"), sodass sie nur bei Reparaturen und in Ausnahmefällen zur Entsorgung anfallen.
Quelle(n):
- Informationszentrum für betrieblichen Umweltschutz [IBU] (2012): Betrieblicher Umweltschutz [online]. Ministerium für Umwelt, Klima und Energiewirtschaft Baden-Württemberg, verfügbar unter: Link
Vermeiden von zu hoher MMS-Dosierung
- In der Regel werden nur sehr geringe Schmierstoffmengen, meist unter 10 ml/h benötigt. Bei diesen kleinen Mengen ist der Sprühstrahl nicht sichtbar, was häufig zu Unsicherheiten beim Maschinenbediener und zur unkontrollierten Erhöhung der Dosierung führt. Die Folge sind Ölablagerungen auf dem Werkstück und im Maschineninnenraum.
- Die Funktionsfähigkeit des MMS-Systems lässt sich mit einem vor die Düse gehaltenen Blatt Papier, auf dem langsam ein kreisförmiger Ölfilm sichtbar werden sollte, einfach nachweisen.
- Bei hochwertigen Systemen sind inzwischen auch ergänzende Flussüberwachungssysteme verfügbar.
- Bei Überdosierung bilden die Ölablagerungen zusammen mit feinen Spänen im Maschineninnenraum eine schmierige bis feste Schicht, die erhöhten Reinigungsaufwand bedeutet. Bei optimaler Einstellung des MMS-Systems kann dieser Effekt vermieden werden. Zur Vermeidung von Staub und Ölnebelemissionen sollte die Werkzeugmaschine an eine Absauganlage mit geeigneter Abscheideeinrichtung angeschlossen sein. Bei der Bearbeitung von Al-Werkstoffen ist zudem die mögliche Brand- u. Explosionsgefahr zu berücksichtigen. Hier sollten die abgesaugten Stäube über einen Nassabscheider abgeschieden werden.
Quelle(n):
- Informationszentrum für betrieblichen Umweltschutz [IBU] (2012): Betrieblicher Umweltschutz [online]. Ministerium für Umwelt, Klima und Energiewirtschaft Baden-Württemberg, verfügbar unter: Link
Verzicht auf Kühlschmierstoffe beim Schleifen
- Bei einem trockenen Schleifprozess fallen statt Schleifschlämmen nur trockene Metallstäube an. Diese sind wesentlich besser metallurgisch verwertbar.
- Die Trockenbearbeitung ist nach heutigen Erkenntnissen nur in Ausnahmefällen möglich, z.B. beim Anschleifen von Planflächen in der Federnherstellung.
- Teilweise können Schleifprozesse auch durch das kühlschmierstofffreie Hartdrehen substituiert werden. Dadurch entfallen alle KSS-bedingten Umweltbelastungen und Kosten.
Quelle(n):
- Informationszentrum für betrieblichen Umweltschutz [IBU] (2012): Betrieblicher Umweltschutz [online]. Ministerium für Umwelt, Klima und Energiewirtschaft Baden-Württemberg, verfügbar unter: Link
Werkzeugbeschichtung: Universallösung für Nass- und Trockenfräsen
"Der Trend geht weg von dicken Katalogen voller Sonderlösungen, hin zu breitflächig einsetzbaren Werkzeugen, schnellem Zugriff und geringere Lagerhaltung"
Werkzeuge mit zielgerichteter Kühlschmierstoff-Zuführung
- die Werkzeuge kühlen punktgenau dort, wo die Kühlung benötigt wird: an der Schneidkante
- Prozesssicherheit, reduzierter Ausschuss und schnellere Bearbeitung und somit eine Steigerung der Effizienz sind die Folge
Umsetzungsbeispiele
Vorausschauende Wartung von Fräsen durch die Analyse akustischer Frequenzspektren
Das folgende Anwendungsszenario beschreibt den Einsatz von KI in der Fertigungslinie zur vorausschauenden Wartung von Fräsmaschinen, die zur Bearbeitung von Stahlbauteilen eingesetzt werden und kann entlang der Wertschöpfungskette in der Produktion eingegliedert werden. Bei diesem Vorgang nutzt sich der Schneidkopf der Fräsmaschinen kontinuierlich ab, wodurch die Schnittgenauigkeit verringert und der Ausschuss erhöht wird. Zusätzlich können der unerwartete Ausfall und die Reparatur von Maschinen den Stillstand von Fertigungsstraßen bedeuten, was zu erheblichen Kosten im Betrieb führen kann.
Durch den Einsatz von KI wird der Zustand der Komponenten der Fräse überwacht und die Restnutzungsdauer bestimmt. Als Datengrundlage dienen hierbei akustische Frequenzspektren, die sich durch das Rotieren des Schneiders ergeben und in Echtzeit übermittelt werden. Mithilfe einer logistischen Regressionsanalyse werden die Frequenzspektren analysiert und mit Soll-Zustandsparametern verglichen. Überschreiten die Abweichungen einen vorher definierten kritischen Wert, so kann die Wartung der Maschine frühzeitig und zu ausgewählten Zeiten eingeleitet werden.
Für den Betrieb ergibt sich der Vorteil, dass die Planungssicherheit hinsichtlich der eingesetzten Fräsen steigt. Verschleiß kann antizipiert und das Wechseln von Schneideköpfen dahingehend geplant werden, dass Qualität und Volumen der Produktion langfristig hoch bleiben. Zusätzlich können erhebliche Kosten eingespart werden, indem ungeplante Stillstandzeiten reduziert werden. [VDI Zentrum Ressourceneffizienz GmbH (2021)]
Maßnahmen:
- M1: Vernetzung von Sensoren und Aktoren
- M7: Zustandsüberwachung
- M8: Prädiktive Wartung
Eingesparte betrieblich materielle Ressourcen:
- Elektrische Energie (gering) Vermeidung von Anlaufprozessen bei Maschinenausfall
- Material (mittel) Verringerung der Ausschussmenge an Stahl
Quelle(n):
- VDI Zentrum Ressourceneffizienz GmbH (2021): Potenziale der schwachen künstlichen Intelligenz für die betriebliche Ressourceneffizienz. VDI Zentrum Ressourceneffizienz GmbH [aufgerufen am: 27.01.2023], verfügbar unter: [S. 71ff] Link
Projekte
BMBF-Forschungsprojekte „Beat“
- In dem Forschungsprojekt "Bewertung der Energieeffizienz alternativer Prozesse und Technologieketten" (Beat) wurden Effizienzsteigerungen bei Zerspanungsprozessen untersucht.
- Im Mittelpunkt standen die Energieeffizienz alternativer zerspanender Technologieketten sowie komplexe Energie- und Stoffströme.
- Es wurde ein Softwaremodul geschaffen, mit dem Anwender ihre Produkte nach DIN EN ISO 14040/44 ökologisch bilanzieren und nach beliebigen Wirkungskategorien – wie z. B. CO₂-Äquivalenz und Primärenergiebedarf – auswerten können.
AEROSPIN – Untersuchungen, Konzeption, Entwicklung und Prototypenfertigung einer innovativenBaureihe von Hochleistungsspindeln
- Entwicklung von Hochleistungsspindeln mit Luftlagertechnik für den Einsatz in der Mikrozerspanung und der Hochpräzisionsbearbeitung
- nahezu unbegrenzte Lebensdauer von Spindel vom Spindelgehäuse durch Luftpolster
- niedrigerer Energieverbrauch
Effizientere Auslegung von Werkzeugmaschinen
- Ergebnis des Verbundprojekts "Energie MSP" war, dass vor allem der Aufbau des Spindelmotors und die Stromspeisung der Antriebe ein großes Potenzial, die Effizienz zu erhöhen, bieten. So könnten z. B. Komponentenhersteller durch Einsatz von Leichtbaumaterialien das Gewicht der Spindeln reduzieren. Dies spart nicht nur Energie beim Beschleunigen und Bremsen, sondern führt auch bei den Vorschubachsen zu einer höheren Energieeffizienz.
- Untersuchungen im Rahmen des "Ewotek"-Verbundprojekts zeigen, dass Kühlschmiermittel-Zufuhr und -aufbereitung, Hydrauliksystem, Kühlsystem und Asynchronmotor für den Spindelantrieb mehr als zwei Drittel des Gesamtenergieverbrauchs einer Werkzeugmaschine verursachen. Durch eine energieeffiziente Regelung und Nutzung dieser Aggregate könnten rund 30 % der bislang verbrauchten Energie eingespart werden.
Effizienzsteigerung durch den Einsatz einer hocheffizienten Schleifmaschine
- Vorzeitiger Ersatz von Schleifmaschinen zur Werkzeugbearbeitung
- Einsatz hocheffizienter CNC-gesteuerter Modelle
- Bedarfsgerechter Betrieb spart bis zu 926 MWh in 10 Jahren ein
Effizienzsteigerung durch hocheffiziente Faserlaser
- CO2-Laser wird durch hochmodernen Faserlaser ersetzt und mit automatisierten Peripheriegeräten ausgestattet
- Stromeinsparung von 1346 MWh innerhalb der Nutzungsdauer von 10 Jahren
Emissionsarmes Feinstschleifen von Keramikwerkstoffen
- Gegenüber dem Läppen entfällt das Entsorgungsproblem des Schleifkorns
- Außerdem erzielt das Schleifen mit gebundenem Korn deutlich höhere Abtragsraten und damit kürzere Bearbeitungszeiten.
Energieeffiziente Zerspanung durch integrierte Absaugung
- In Zerspanungsmaschine integrierte Absaugeinrichtung für Holz- und Kunststoffverarbeitung
- Absaugung soll an individuellen Zerspanungsprozess angepasst werden für maximale Energieeffizienz
- System ist flexibel bei verschiedenen Maschinen nachrüstbar
Entwicklung eines produktionsintegrierten Verfahrens zur MICROFINISH-Oberflächenfeinstbearbeitung unter Substitution der überfluteten Kühlschmierung durch umweltfreundliche Minimalmengenschmiertechnik
- Schleifung wellenförmiger Teile ohne Zerspanungshilfsstoff
Forschungsprojekt eApps4Production
- reale Zustands- sowie Prozessdaten unterschiedlicher Systeme in einer Oberfläche nutzbar machen
- föderative Gestaltung ermöglicht gemeinsame Nutzung durch verschiedene Teilnehmer
- entstehende Plattform bietet auch KMU neue Möglichkeiten zur Entwicklung eigener eApps
Harte Werkstoffe mit langer Lebensdauer
- Entwicklung einer neuen Klasse von Verbundwerkstoffen und Verschleißschutzschichten aus einer harten Wolframcarbid- und einer duktilen metallischen Bindephase
- Einsatz von modernen Sintertechnologien wie druckunterstützter Kurzzeitsinterverfahren zur Herstellung polykristalliner Hartmetalle aus rezykliertem und synthetisiertem Wolframcarbid mit verschiedenen Cobaltgehalten
- Verringerung der Rohstoffabhängigkeit und bis zu 100 % Verwertungsrate von binderfreiem Wolframcarbid-Schrott
Innovative Fertigungstechnologie zur Herstellung von Gewindewerkzeugen
- Implementierung einer innovativen Fertigungstechnologie für Gewindewerkzeuge
- Verbesserung der Oberflächen- und Schneidkantenbeschaffenheit und Verringerung der Reibung zwischen Werkzeug und Werkstückwerkstoff
- Implementierung einer automatisierten Nassstrahlanlage für das gesamte Produktportfolio
Maximierung der Energieeffizienz von Werkzeugmaschinen (MAXIEM)
- Bei dem Ende 2012 abgeschlossenen Projekt Maxiem konnte den Energieverbrauch einer Demonstratormaschine um rund 50 % zu senken.
- Optimiert wurden beispielsweise Hydraulik und Druckluft, Schaltschrankklimatisierung, Maschinenkühlung, Kühlschmierung und Absaugung. Bezogen auf einen 3-Schicht-Betrieb mit sechs Arbeitstagen pro Woche (ohne Standby) konnte der Energieverbrauch von 101.547 auf 48.620 kWh/a reduziert werden.
Potenziale des Trockenschleifens
- Aluminiumoxid- u. Bornitrid-Schleifscheiben sind bei angepasster Prozessgeometrie u. -führung grundsätzlich geeignet für Trockenschleifverfahren
- Durch eine Minimalmengenschmierung lassen sich bessere Oberflächenqualitäten bei geringerer Randzonenbeeinflussung erreichen, ohne dass diejenigen Probleme auftreten, die mit dem Einsatz großer Mengen von Kühlschmierstoff einhergehen.
- Die Ergebnisse der Versuche sind in einer umfangreichen Datensammlung und Empfehlungen für Prozessparameter dokumentiert.
Projekt NCplus: Energie verstärkt für die Zerspanung einsetzen
- Das Hauptziel des Projekts ‚NCplus‘ war, den Energieanteil zu erhöhen, der für die Arbeit unmittelbar am Werkstück aufgewendet wird, und gleichzeitig den Gesamtverbrauch um 30 % zu senken.
- Die im Projekt entwickelten Lösungen reichen von der Optimierung von Komponenten für die Kühlung und der Hydraulik-Anlage bis hin zur Entwicklung einer effizienten Frässpindel und einer spielfreien Haltebremse.
Trockenbearbeitung beim Wirbeln
- kühlschmiermittelfreie bzw. minimal geschmierte Zerspanung beim Wirbeln ist möglich
- Verfahrensmodell, mit dessen Hilfe unterschiedliche Zerspanungsbedingungen, insbesondere die Prozessführung ohne Kühlschmierstoff, simuliert werden können.
- Welche Variante in der Praxis zum Einsatz kommt, ist von fertigungstechnischen und wirtschaftlichen Gesichtspunkten abhängig.
Trockenbearbeitung beim Wirbeln: Beschichtetes Hartmetall zum Wirbeln
- Trockenzerspanungsverfahren „Wirbeln“ führt zur Einsparung von Kühlschmierstoffen, Rohstoffen u. Energie
- Testen und Entwicklung von Hartmetallschneidstoffen
- Die Entwicklungen wurden ergänzt mit der Untersuchung des Einflusses der Schneidkantenmikrogeometrie auf die Schneidleistung der Werkzeuge.
Umweltgerechte Zerspanung durch den Einsatz der Minimalschmiertechnik beim Wälzfräsen
- Minimalschmiertechnik als gleichwertige Alternative zur Vollstrahltechnik
- Durch die geringen Mengen an eingesetzten Kühlschmierstoffen entfallen beispielsweise die Entsorgungsvorgänge komplett.
- Amortisation der Anlagentechnik: ca. 2 Jahre
VDMA-Initiative Blue Competence
- Stellschrauben für eine deutliche Energiedrosselung an Werkzeugmaschinen sind beispielsweise der Einsatz energieeffizienter Maschinenkomponenten, ein energiebewusster Maschineneinsatz durch Stand-by-Betrieb sowie die Steigerung der Produktivität.
- Kürzere Fertigungszeiten reduzieren den Energieverbrauch.
Wasserbasierter Kühlschmierstoff für eine Minimalmengenschmierung bei zerspanenden Verfahren
- Entwicklung eines Hochleistungskühlschmierstoff für die Minimalmengenschmierung beim Bohren
- Auswahl und Erprobung einer optimalen Fluidrezeptur durch Langzeitversuche und Korrosionstests
- Ökologische und performante Vorteile gegenüber herkömmlichen Kühlschmierstoffen
Videos
Berater mit Mission
Mit dem Aufruf des Videos erklären Sie sich einverstanden, dass Ihre Daten an YouTube übermittelt werden und dass Sie die Datenschutzerklärung gelesen haben.
Aufarbeitung KSS
Beste verfügbare Technik
Abtrennung und Rückführung von mit dem Schleifschlamm ausgetragener KSS
- Ziele einer innerbetrieblichen Vorbehandlung von Schleifschlämmen:
- Austragsverluste möglichst gering halten
- Entsorgungsmengen reduzieren und
- Verwertungsmöglichkeiten des Schleifschlamms durch reduzierten Öl- u. Fremdstoffgehalt verbessern
- Mit den Schleifschlämmen werden bis zu 60 % an Kühlschmierstoffen aus dem Maschinenkreislauf ausgetragen. Pro Tonne Schleifschlamm gehen damit bis zu 600 Liter KSS verloren. Insbesondere bei Verwendung von KSS-Ölen ist daher eine Entölung mit Ölrückführung finanziell interessant.
- Bei moderaten Investitionen sind bereits bei Anfallmengen von 10 t/a Amortisationszeiten von unter 2 Jahren zu erzielen.
- Wenn möglich, sollten hilfsmittelfreien Filtrationsverfahren (z.B. Umlaufbandfilter, Trommelspaltfilter, rückspülbare Filtersysteme (ohne Anschwemmmittel!), Zentrifugen, Absetzbecken mit mechanischem Schlammaustrag usw.) zum Einsatz kommen.
- Bei der Systemauswahl ist auf einen (möglichst niedrigen) Restöl-/Restfeuchtegehalt des Schleifschlamms und geringen Energieverbrauch zu achten.
- Bei der Verarbeitung ferromagnetischer Werkstoffe können Magnetabscheider eingesetzt werden. Für die Entfernung nichtmagnetischer Inhaltsstoffe muss jedoch ein zusätzliches Filtersystem installiert werden.
- Umgehend (d.h. möglichst ohne längere Zwischenlagerung) aus den Schlämmen abgetrennte KSS-Öle können in der Regel direkt in den KSS-Kreislauf zurückgeführt werden. Bei KSS-Emulsionen u. -Lösungen sollte in Rücksprache mit dem KSS-Lieferanten geprüft werden, ob sie wieder eingesetzt werden können.
- Für die betriebsinterne Entwässerung/ Entölung stehen in der Praxis im Wesentlichen die 3 Verfahren zur Verfügung: Entwässerung im Sammelcontainer, Abpressen und Zentrifugieren. Eine weitergehende Entölung ist zwar technisch möglich, wegen der hohen Investitionskosten jedoch nur bei sehr großen Mengen, d. h. in externen Zentralanlagen, wirtschaftlich realisierbar.
Quelle(n):
- Informationszentrum für betrieblichen Umweltschutz [IBU] (2012): Betrieblicher Umweltschutz [online]. Ministerium für Umwelt, Klima und Energiewirtschaft Baden-Württemberg, verfügbar unter: Link
Bakterizidfreie Kühlschmierstoffe
- der Einsatz bakterizidfreier Kühlschmierstoffe sorgt für hohe Stabilität und niedrigen Verbrauch
Erhöhen der Badstandzeiten von KSS
- Durch präventive Maßnahmen, geeignete Pflege in Kombination mit einer regelmäßigen Überwachung lassen sich die Badstandzeiten oft erheblich verlängern.
- Mit geeigneten Badpflegemaßnahmen (Abtrennung von Fremdölen, Entfernung von Feststoffen, ausreichende Belüftung und erforderlichenfalls Kühlung) lassen sich gute Badstandzeiten erzielen: als Anhaltswerte gelten ½ Jahr für einzelversorgte Maschinen und 2-3 Jahre bei Zentralanlagen. Somit haben Zentralanlagen den Vorteil eines deutlich geringeren Abfallaufkommens, in der Regel verbunden mit Vorteilen beim Arbeitsschutz durch bessere Pflege- u. Überwachungsmöglichkeiten.
- KSS-Öle (nichtwassermischbare KSS) sind in der Beschaffung vergleichsweise teuer, bezüglich der Kreislaufführung jedoch relativ einfach zu handhaben und weisen in der Regel sehr lange Standzeiten auf. Die Badpflege beschränkt sich meist auf die Entfernung der Späne (Spänesieb) und die Abfiltrierung der Feinanteile (Schleifschlamm), sowie erforderlichenfalls eine Temperierung. Die üblichen Standzeiten liegen bei 5-10 Jahren. Bei der Filtrierung sollte nach Möglichkeit ein hilfsmittelfreies Filtersystem eingesetzt werden.
- Deutlich komplexer gestaltet sich die Badpflege bei wassergemischten KSS (Emulsionen, Lösungen). Durch den hohen Wasseranteil, verbunden mit organischen Inhaltsstoffen (Öle, Emulgatoren usw.) sind Emulsionen und Lösungen wesentlich empfindlicher gegen Fremdstoffeinträge und neigen zur Verkeimung. Nur mit geeigneten Badpflegemaßnahmen (Abtrennung von Fremdölen, Entfernung von Feststoffen, ausreichende Belüftung und erforderlichenfalls Kühlung) lassen sich gute Badstandzeiten erzielen. Als Anhaltswerte gelten hier ½ Jahr für einzelversorgte Maschinen und 2-3 Jahre bei Zentralanlagen.
- gerade bei Badstandzeiten im Wochenbereich sind Optimierungsmaßnahmen mit einer deutlichen Kostenreduzierung verbunden
Quelle(n):
- Informationszentrum für betrieblichen Umweltschutz [IBU] (2012): Betrieblicher Umweltschutz [online]. Ministerium für Umwelt, Klima und Energiewirtschaft Baden-Württemberg, verfügbar unter: Link
Getrennte Sammlung
Nach der Konditionierung ist in der Regel eine metallurgische Verwertung möglich. Bei verschiedenen Schleifschlammqualitäten sollte die betriebsinterne Erfassung so erfolgen, dass die Annahmekriterien der verfügbaren Verwertungsanlagen (Werkstoffgruppen, Ölgehalt, Schadstoffe) eingehalten werden können.
Quelle(n):
- Informationszentrum für betrieblichen Umweltschutz [IBU] (2012): Betrieblicher Umweltschutz [online]. Ministerium für Umwelt, Klima und Energiewirtschaft Baden-Württemberg, verfügbar unter: Link
Minimalmengen-Schmierung (MMS)
- eine Alternative zum Kühlschmierstoff (KSS)-Einsatz ist die Trockenbearbeitung bzw. die Minimalmengen-Schmierung (MMS): kleinste Mengen Kühlschmierstoff werden dabei genau an die Stelle gebracht, wo sie benötigt werden.
- Vorteile:
- viel geringerer Schmierstoffverbrauch
- keine Verunreinigung im Umgebungsbereich der Maschine, auch die Maschinen bleiben sauberer
- die Werkstücke bleiben sauber (ölfrei)
- die Werkstückreinigung vor einer nachfolgenden Lackierung wird einfacher, kann teilweise sogar entfallen.
- Insbesondere bei Säge- u. Fräsoperationen von Aluminium lassen sich Kühlschmierstoffe gut durch die MMS substituieren.
- Bei der Profilbearbeitung können durch die Substitution von KSS große Erfolge erzielt werden, da erhebliche Mengen an KSS allein dadurch ausgetragen, dass sie an und in den Profilen ablaufen. Die Folge sind verschmutzte Bereiche rund um die Maschine, KSS-Lachen auf dem Boden, hohe KSS-Verluste und nicht zuletzt verölte Teile, die aufwendig wieder gereinigt werden müssen.
- bestehende Maschinen können nachgerüstet werden (z.B. mit einem einfachen MMS-System (Microjet))
- Realisierungsmöglichkeiten der MMS sollten bei Neuinvestitionen geprüft werden.
Quelle(n):
- Informationszentrum für betrieblichen Umweltschutz [IBU] (2012): Betrieblicher Umweltschutz [online]. Ministerium für Umwelt, Klima und Energiewirtschaft Baden-Württemberg, verfügbar unter: Link
Rückführung der ausgetragenen KSS-Öle (Schleifen)
- Auch bei kleinen Anlagen können mit einfachen Maßnahmen oft erhebliche Kosteneinsparungen z.B. durch Rückführung der über Späne und Teile ausgetragenen Öle realisiert werden (z.B. Spänekarren mit Ablasshahn für KSS).
- Je nach Austragssystem können z.B. Messingspäne bis zu 30 % und Schleifschlämme bis zu 70 % Kühlschmierstoff enthalten.
- Spänebehälter sollten daher einen Ablasshahn für ablaufende Kühlschmierstoffe haben. Bei größerem Späneanfall kann eine Zentrifuge rentabel sein.
- KSS-Öle können direkt in den Maschinenkreislauf zurückgeführt werden (ggf. über einen Filter), bei Emulsionen sollte vorher geprüft werden, ob die Emulsion noch gebrauchsfähig ist.
Quelle(n):
- Informationszentrum für betrieblichen Umweltschutz [IBU] (2012): Betrieblicher Umweltschutz [online]. Ministerium für Umwelt, Klima und Energiewirtschaft Baden-Württemberg, verfügbar unter: Link
Trockenbearbeitung - Eine Technologie zur Steigerung der Ökoeffizienz bei der Metallbearbeitung
- Durch den Verzicht auf Kühlschmierstoffe (KSS) oder durch die Minimalmengen-Schmierung (MMS) lassen sich viele Vorteile erzielen, sowohl in Bezug auf Effizienzsteigerung und Kostenersparnis als auch in Bezug auf eine nachhaltige Verbesserung der betrieblichen Umweltsituation und der Arbeitsplatzqualität:
1) Vermeidung KSS-bedingter Kosten
- kein oder minimaler KSS-Bedarf
- reduzierte Investitionen (Behälter, Pumpen, Rohre, Pflegeeinrichtungen)
- keine KSS-bedingten Abfälle mehr (z.B. verbrauchte KSS, ölhaltige Späne und Schleifschlämme, Filtervliese, Ölbindemittel, Putzlappen usw.)
- preiswertere Späneentsorgung
- Keine KSS-Überwachung u. -Wartung
- Saubere Umgebung und Teile
- Bessere Sicht auf den Bearbeitungsvorgang und verbesserter Arbeitsschutz und Arbeitshygiene
2) Steigerung der Bearbeitungseffizienz
- schnellere Bearbeitung möglich
- keine Thermoschockbelastung der Optimierung der Prozessabläufe
- bei sauberen Teilen kann ggf. auf Reinigungsprozesse verzichtet werden
- weniger Nebenprozesse
3) Werkzeuge (Standzeiterhöhung)
- Geringerer Platzbedarf
- Weniger Nebentätigkeiten
4) Umweltaspekte der Trockenbearbeitung
Quelle(n):
- Informationszentrum für betrieblichen Umweltschutz [IBU] (2012): Betrieblicher Umweltschutz [online]. Ministerium für Umwelt, Klima und Energiewirtschaft Baden-Württemberg, verfügbar unter: Link
Vereinheitlichung von KSS
- Haben Sie mehrere KSS gleichen Typs (Öle, Emulsionen oder Lösungen) im Einsatz, so sollten Sie die Möglichkeiten einer Vereinheitlichung überprüfen.
- Häufig sind durch gewachsene Strukturen (zu) viele KSS-Produkte im Einsatz. In Abhängigkeit vom Bearbeitungsspektrum kann die KSS-Produktpalette meist eingeschränkt werden (Zielsetzung: 1 Emulsion, 1 Lösung, maximal 2 Öle).
- Neben der Voraussetzung für eine Zentralversorgung hat die Vereinheitlichung folgende Vorteile: Einfachere Lagerung, verbesserte Logistik, geringere Verwechslungsgefahr, Wegfall von Zwischenreinigungsprozessen. Zentralanlagen werden heute im Größenbereich von 2 bis 100m³ eingesetzt. Das Volumen richtet sich nach dem durchschnittlichen KSS-Bedarf der angeschlossenen Maschinen. Als Richtgröße gilt für wassergemischte KSS eine Umlaufzahl (umgewälztes Badvolumen pro Stunde) von 6-10.
Quelle(n):
- Informationszentrum für betrieblichen Umweltschutz [IBU] (2012): Betrieblicher Umweltschutz [online]. Ministerium für Umwelt, Klima und Energiewirtschaft Baden-Württemberg, verfügbar unter: Link
Vermeidung von Reinigungsaufwand (KSS)
- Durch Verdampfungs-, Spritz- u. Austragsverluste wird nahezu der gesamte spanende Fertigungsbereich in irgendeiner Form vom KSS-Einsatz tangiert. Dies betrifft insbesondere den Einsatz von KSS-Ölen. Die Austragsverluste über Späne und Werkstücke sind durch die höhere Ölviskosität höher. Entstehende Ölnebel u. -Dämpfe schlagen sich an Maschinen, am Boden und an Gebäudeeinrichtungen nieder.
- Maßnahmen, die den Reinigungsaufwand und die damit verbundenen Abfälle (Ölbindemittel, Putzlappen, Reinigungsmittel) sowie die Verschleppungsverluste reduzieren:
- für die bearbeiteten Bauteile Abtropfzonen einrichten, schöpfende Teile drehen
- Späne ebenfalls abtropfen lassen (Lochblech mit Absaug- bzw. Ablassmöglichkeit im Spänekontainer)
- Bei hohem Ölaustrag kann sich eine Spänezentrifuge rentieren, auch unempfindliche Teile lassen sich zentrifugieren. Das KSS-Öl kann wieder in den Maschinenkreislauf zurückgeführt werden.
- Bei der KSS-Auswahl auch auf nebelarme KSS-Qualitäten achten
- Eine gute Kapselung des Bearbeitungsraums (für neue Werkzeugmaschinen Pflicht) mit geeigneter Absaugung reduziert die Verdampfungsverluste und damit den Reinigungsaufwand
- Bei wassergemischten KSS sind die Austragsverluste in der Regel geringer, die Verdampfungsverluste betreffen vorwiegend den Wasseranteil.
- Nur durch Trockenbearbeitung bzw. Minimalmengen-Schmierung lassen sich die KSS-Verluste gänzlich vermeiden. Insbesondere bei Neuinvestitionen sollten daher die Realisierungsmöglichkeiten der Trockenbearbeitung geprüft werden.
Quelle(n):
- Informationszentrum für betrieblichen Umweltschutz [IBU] (2012): Betrieblicher Umweltschutz [online]. Ministerium für Umwelt, Klima und Energiewirtschaft Baden-Württemberg, verfügbar unter: Link
Projekte
Kühlschmierstoffe – es geht auch ohne
- Technologienetz und ein Industriearbeitskreis zum Thema Trockenbearbeitung bei der Metallzerspanung
- Technologietransfer in Richtung kleiner und mittelständischer Unternehmen
Abfall- und Abwasserbehandlung
Beste verfügbare Technik
Innerbetriebliche Behandlung von Schleifschlämme
- Ölhaltige Schleifschlämme fallen nahezu bei allen spanenden Metallbearbeitungsprozessen an. Sie resultieren nicht nur aus Schleif-, Hon- und ähnlichen Prozessen, sondern auch als Feinfraktion aus der Filtration der Kühlschmierstoffe (KSS) in der spanenden Bearbeitung allgemein.
- Schleifschlämme sind gefährliche Abfälle. Konsistenz und Inhaltsstoffe (feine Metallpartikel, Schleifmittelabrieb, KSS, eventuell Filterhilfsmittel) schwanken, abhängig vom Entstehungsprozess sowie den verarbeiteten Werk- u. eingesetzten Hilfsstoffen in großer Bandbreite. Für die Beseitigung und insbesondere für die Verwertung ist die Kenntnis der Zusammensetzung und der Konsistenz wichtig.
- In vielen Betrieben fallen unterschiedliche Schleifschlammqualitäten an. Für eine Verwertung ist eine sortenreine Erfassung und Lagerung von Bedeutung:
- Hartmetallschlämme separat sammeln (Vergütung vom Entsorger)
- Stark ölhaltige Schleifschlämme getrennt halten von Schleifschlämmen aus der Bearbeitung mit KSS-Emulsionen o. -Lösungen
- Schleifschlämme und Filterhilfsmittel (insbesondere Filtervliese) nach Möglichkeit getrennt erfassen
Quelle(n):
- Informationszentrum für betrieblichen Umweltschutz [IBU] (2012): Betrieblicher Umweltschutz [online]. Ministerium für Umwelt, Klima und Energiewirtschaft Baden-Württemberg, verfügbar unter: Link
Nach Werkstoffen getrennte Sammlung von Spänen und Metallabfällen
Falls neben Baustählen auch hochlegierte Stähle (VA-Qualitäten, Nickellegierungen) verarbeitet werden, so sollten die anfallenden Späne und sonstigen Metallabfälle nach Möglichkeit getrennt erfasst werden. Die Vergütungen für sortenreine Späne und Metallabfälle sind deutlich höher als für Mischfraktionen. Bei kleinen Mengen eignen sich dazu z.B. ausgemusterte 200 l-Fässer.
Quelle(n):
- Informationszentrum für betrieblichen Umweltschutz [IBU] (2012): Betrieblicher Umweltschutz [online]. Ministerium für Umwelt, Klima und Energiewirtschaft Baden-Württemberg, verfügbar unter: Link
Projekte
Aufbereitung von Schleifschlämmen und Wiedernutzbarmachung ihrer Bestandteile: Koordination und Schmelzaufbereitung
- Entwicklung eines neuartigen Verfahrens- u. Anlagenkonzeptes, um Schleifschlamm-Bestandteile wirtschaftlich in flüssige und feste Anteile zu trennen und zu Wertstoffen aufbereiten zu können
- In die Untersuchungen wurde der Status quo bei Schleifschlamm-Anfall, -Behandlung u. –Entsorgung aufgenommen
- Ergebnis: neue Verfahrens- und Anlagenkombination (Trocknung/Entölung des Schleifschlamms; Brikettierung; metallurgische Verwertung des entölten Schleifschlamms)
- zur Erhöhung der Marktfähigkeit des aufbereiteten Schleifschlamm-Feststoffs wurde ein innovatives Brikettier-Verfahren entwickelt: herausragende Merkmale sind eine hohe Festigkeit der Briketts ohne Vermischung mit anderen Wertstoffen (z. B. Drehspäne)
- zurückgewonnene Kühlschmierstoffe können teilweise (ggf. nach Zusatz von Additiven) in Schleifprozesse zurückgeführt werden
Errichtung eines Produktionswerkes zur umweltschonenden Produktion von Betonelementen
- Reduzierung von Schleifwasseranfall und Staubemission durch neue Technologie
Kombinierte mechanisch-thermische Entölung zur innerbetrieblichen stofflichen Aufbereitung von Schleifschlämmen in der Metallindustrie
- der Restölgehalt des Schleifschlamms wurde gesenkt und die Menge des zurückgewonnenen Schleiföls gesteigert
- Durch die guten Entölungsergebnisse bei Anwendung der mechanisch-thermischen Entölung ergibt sich insbesondere für KMU die Möglichkeit einer Rückgewinnung der Schleiföle. Betriebsmittelkosten können dadurch merklich gesenkt werden. Des Weiteren eignen sich die stark entölten Schleifschlamm-Presslinge für eine metallurgische Verwertung, beispielsweise in Gießereien, und stellen somit ein interessantes Produkt für die Schmelzbetriebe dar. Auch dies trägt zu einer deutlichen Verringerung der Entsorgungskosten in den Metallbearbeitungsbetrieben bei.
Produktionsanlage zur Trockenbearbeitung von Aluminiumrädern und -Teilen mit geschlossener Kreislaufführung der Al-Späne
- Realisierung des Produktionsbereichs „mechanische Bearbeitung“ unter der Vorgabe der Trockenbearbeitung (Innen- u. Außendrehen, Entgraten, Bohren)
- Verzicht auf KSS-Einsatz gesamten Fertigungsbereich; somit ist weder eine KSS-Versorgung noch eine Abwasserbehandlung erforderlich
- Einsparung von ca. 700 m³/a verbrauchter KSS-Emulsion, ca. 4.200 kg/a Chemikalien, ca. 200 m³/a Abwasse
- der Energiebedarf konnte unter Einbeziehung der Nebenprozesse um ca. 40 % reduziert werden
- beim Wiedereinschmelzen der Al-Späne in der Gießerei werden die Emissionen deutlich reduziert
Umstellung eines Fertigungsbereichs auf Trockenbearbeitung
- Umstellung eines ganzen Fertigungsbereichs mit mehreren Werkzeugmaschinen auf Trockenbearbeitung in einem mittelständischen Unternehmen
- verbesserte Abfallsituation durch den Verzicht auf Kühlschmierstoff (die Späne sind praktisch ölfrei und der Anteil anderer ölhaltiger Abfälle verringert sich um ca. 97 %)
Externe Verwertung
Beste verfügbare Technik
Schleifschlämme - Verwertungsmöglichkeiten
Der Öl- bzw. Kohlenwasserstoff-Gehalt ist einer der wichtigsten Parameter für die Nutzbarkeit einer Verwertungs- oder auch Beseitigungsschiene. In vielen Fällen ist zur Realisierung von stofflichen Verwertungsmöglichkeiten eine vorherige Entölung/ Konditionierung der Schleifschlämme unumgänglich. Anlagen hierzu sind teilweise kommerziell verfügbar oder befinden sich in der Erprobung:
- Brikettierung: Vorwiegend für emulsionshaltige Schleifschlämme geeignet. Die Späne werden mit ca. 20 % Schleifschlämmen gleicher Werkstoffsorte vermischt und zu mechanisch belastbaren Briketts verpresst (Mischbrikettierung). Die Restölgehalte liegen dabei unter 2 %, sodass die Briketts in Stahlwerken und Gießereien eingeschmolzen werden können.
- Sinterung: Je nach Anlagenauslegung mit unterschiedlichen Annahmekriterien.
- Entölung durch Vakuum-Trocknung: Vorwiegend für hochölhaltige Schleifschlämme (abgetrennte Öle können teilweise als KSS wieder eingesetzt werden)
- Entölung durch Ausbrennen der organischen Bestandteile. Ausgelegt für mittlere Ölgehalte, wobei der Ölanteil verloren geht.
- Entölung mittels überkritischer Kohlendioxid-Extraktion: Vorwiegend für hochölhaltige Schleifschlämme (abgetrennte Öle können als KSS wieder eingesetzt werden). Das Verfahren wurde bisher nur im Technikumsmaßstab realisiert.
Verwertung der Metallkomponente:
- Verhüttung (Hochofen)
- Einsatz in Stahlwerken/Gießereien (vorherige Entölung/Konditionierung erforderlich)
- Rückgewinnung hochwertiger Legierungselemente (VA-Stähle, Hartmetalle)
- Fe-Zuschlag in Zementwerken
Für die aufgeführten Verwertungswege sind überwiegend große Mengen bekannter Zusammensetzungen interessant. Die Zusammenstellung zu großen Chargen erfolgt daher in der Regel durch Recyclingbetriebe der Schrottwirtschaft und Betreiber von Konditionierungs- u. Entölungsanlagen, die damit Ansprechpartner für die Betriebe sind.
Quelle(n):
- Informationszentrum für betrieblichen Umweltschutz [IBU] (2012): Betrieblicher Umweltschutz [online]. Ministerium für Umwelt, Klima und Energiewirtschaft Baden-Württemberg, verfügbar unter: Link
Projekte
Lose Dämmstoffe aus Holz: Herstellung von Dämmstoffspänen aus industriellen Hobelprozessen
- Im Rahmen eines Verbundvorhabens wurde untersucht, ob bzw. unter welchen Bedingungen Spangut als loser Dämmstoff verwertbar ist. In diesem Teilprojekt wurden dazu die Grundlagen zur Spanbildung herkömmlicher Fräsprozesse dargestellt. Insbesondere galt es, den Prozess „Hobeln“ dahingehend zu optimieren, dass bereits bei der Holzverarbeitung geeignete Hobelspäne für die Wärmedämmung entstehen.
Pulvermetallurgische Verwertung aufbereiteter Schleifschlämme
- Ermittlung der vorhandenen Schleifschlammmengen u. –qualitäten sowie die Formulierung von Anforderungen, die für eine Verwertung auf hohem Wertschöpfungsniveau an Pulver aus entölten Schleifschlämmen zu stellen sind
- Ergebnisse: zwischen Primärrohstoffen für die Metallgewinnung und Werkstoffen aus der Schleifschlammaufbereitung zeigte sich ein großer qualitativer Abstand
- Für die Sammlung und höherwertige Verwertung der Schleifabfälle können folgende Anforderungen gestellt werden:
- Die Quelle muss genau bekannt (Ausgangswerkstoffe, Fertigungsschritte) und eine sortenreine Sammlung gewährleistet sein.
- Der Schleifschlamm darf keine Filterhilfsmittel oder andere zusätzliche Verunreinigungen fester Art enthalten.
- Lagerung und Transport der Schleifschlämme müssen kontrolliert erfolgen.
- Die Entölung ist möglichst vollständig durchzuführen.
Prozessperipherie und übergeordnete Maßnahmen
Beste verfügbare Technik
Abfallvermeidung
- durch Trockenbearbeitung: Vorteil der Trockenbearbeitung ist, dass neben der Vermeidung KSS-bedingter Abfälle (verbrauchte Kühlschmierstoffe, Putzlappen, Ölbindemittel usw.) teilweise ganze Prozessschritte eingespart werden können (z.B. Reinigung der Werkstücke), der Reinigungsaufwand für die Maschine und der Umgebung reduziert und Bearbeitungszeiten verkürzt werden.
- durch alternative Formgebungsverfahren: Neben der Trockenbearbeitung sollten auch weitere abfallarme Formgebungsverfahren, wie z. B. Strangpressen, Pulvermetallurgie oder Feinguss als Alternativen zur spanenden Formgebung die in die Überlegungen mit einbezogen werden. Sie kommen jedoch meist nur bei großen Stückzahlen in Betracht.
Quelle(n):
- Informationszentrum für betrieblichen Umweltschutz [IBU] (2012): Betrieblicher Umweltschutz [online]. Ministerium für Umwelt, Klima und Energiewirtschaft Baden-Württemberg, verfügbar unter: Link
Auswahlkriterien für Maschinen- und Hydrauliköle
- Einbeziehung aller Beteiligten: Einbeziehung aller betriebsinternen und externen Beteiligten bei der Öl-Auswahl, z.B. Einkauf, Produktion, Umweltbeauftragte, Öl-Hersteller, Maschinenhersteller, Verwerter und Entsorger, sowie unabhängige Informations- u. Beratungsmöglichkeiten.
- Reduzierung der Produktvielfalt: Reduzieren der Anzahl verschiedener Schmierstoffe und Hydrauliköle. Neben einer vereinfachten Logistik liegen Vorteile bei besseren Verwertungsmöglichkeiten und damit Vorteile vor allem im Kostenbereich.
- Chemikalienabstimmung: Eingesetzte Maschinen- u. Hydrauliköle sollten mit anderen in der Fertigungslinie eingesetzte Chemikalien, mit denen Vermischungen möglich und sind, abgestimmt sein. Dies betrifft in erster Linie Hydraulik- u. Bettbahnöle, die über Leckagen und Auswaschungen in die Kühlschmierstoffe gelangen. Eine Einbindung des Schmierstofflieferanten ist sinnvoll.
Quelle(n):
- Informationszentrum für betrieblichen Umweltschutz [IBU] (2012): Betrieblicher Umweltschutz [online]. Ministerium für Umwelt, Klima und Energiewirtschaft Baden-Württemberg, verfügbar unter: Link
Betrachtung der gesamten Fertigungskette
Die Betrachtung der Fertigungskette, in die das jeweilige Bearbeitungsverfahren eingebunden ist, ist hinsichtlich der Effizienzsteigerung von erheblicher Bedeutung. Einflüsse aus vorgeschalteten Bearbeitungsprozessen sind ebenso zu berücksichtigen wie die Auswirkungen der verwendeten Bearbeitungs- u. Hilfsstoffe auf die Folgeprozesse.
Beispiele:
- Auf Halbzeugen oder Vorprodukten aufgetragene Korrosionsschutzmittel können negative Einflüsse auf die Wirkung von Kühlschmierstoffen und damit die Bearbeitungsqualität haben und zu kurzen Badstandzeiten, zusätzlichen Hautbelastungen bei den Mitarbeitern und zu einem erhöhtem Abfallaufkommen führen.
- Die bei der spanenden Bearbeitung eingesetzten Kühlschmierstoffe werden über die Werkstücke aus dem Prozess ausgetragen und haben damit wiederum erhebliche Auswirkungen auf den Folgeprozess, sei es ein Reinigungsprozess oder ein weiterer Prozess
zur Oberflächenbehandlung.
Eine ganzheitliche Prozessbetrachtung ist Voraussetzung für eine abfallarme und umweltgerechte Produktion und vermeidet Zusatzkosten. Insbesondere müssen Betriebs- u. Hilfsstoffe, die in einer Prozessstufe in Kontakt kommen oder miteinander vermischt werden auf ihre Chemikalienverträglichkeit geprüft und abgestimmt werden. Andernfalls können Unverträglichkeiten z.B. bei KSS- oder Reinigungsbädern zu vorzeitiger Unbrauchbarkeit mit entsprechenden Qualitätsproblemen bei der Produktion oder durch vorzeitigen Austausch zu erhöhtem Abfallaufkommen führen:
- KSS, Hydrauliköle und Bettbahnöle müssen aufeinander abgestimmt sein.
- Korrosionsschutzmittel sind teilweise nitrithaltig. Bei Eintrag in eine KSS-Emulsion steigt daher der Nitrit-Gehalt der Emulsion sehr schnell an. Wegen Überschreitung des Grenzwerts und der Gefahr der Nitrosaminbildung muss das KSS-Bad vorzeitig ausgetauscht werden.
- Insbesondere wässrige Reinigungs- u. Entfettungsbäder müssen auf den abzureinigenden KSS abgestimmt werden. Unterschiedliche Emulgatorsysteme können ebenso zu schnellen Wirkungsverlusten führen wie Öleinträge in ein emulgierendes Reinigungsbad.
- Abstimmung der Hilfsstoffe mit allen Beteiligten: Chemikalienlieferanten, Maschinenhersteller, Einkauf, beteiligte Produktionsabteilungen und ggf. auch Entsorger
- Auch Nebenprozesse wie z.B. die Abwasserbehandlung werden von den eingesetzten KSS maßgeblich (positiv oder negativ) beeinflusst (Beispiel: Zur Emulsionsspaltung mittels Ultrafiltration (aus Wirtschaftlichkeitsgründen nur bei großen Mengen empfehlenswert) hat sich die Vermischung und gemeinsame Behandlung von KSS- u. Reinigungsemulsionen in der Regel bewährt, da die Ultrafiltration von Emulsionsmischungen besser durchzuführen ist.)
Quelle(n):
- Informationszentrum für betrieblichen Umweltschutz [IBU] (2012): Betrieblicher Umweltschutz [online]. Ministerium für Umwelt, Klima und Energiewirtschaft Baden-Württemberg, verfügbar unter: Link
Direktantriebe
- steigern Schnelligkeit und Präzision und steigern somit die Effizienz und reduzieren Ausschuss
Energieeffizienz bei Gleitschleifanlagen
Ansatzpunkte zur Verbesserung der Energieeffizienz bei Gleitschleifanlagen sind:
- Eine energetisch deutlich günstigere Alternative zur Zentrifuge sind Lamellenschrägklärer. Nachteilig ist der größere Platzbedarf und ein deutlich größeres Volumen an Kreislaufwasser.
- Zentrifugen haben einen erheblichen Energiebedarf. Achten Sie auf die Energieffizienz. Betreiben Sie die Zentrifuge im Chargenbetrieb (nicht immer mitlaufen lassen) und nur zur Entfernung des Feinanteils. Gröbere Partikel besser über Sedimentationsverfahren aus dem Kreislauf ausschleusen. Reinigen Sie die Zentrifuge regelmäßig, insbesondere im Trennspalt (Reduzierung der Reibungsverluste).
- Setzen Sie nach Möglichkeit Antriebsmotore des höchsten Energieeffizienzniveaus ein.
- Druckluftbetriebene Membranpumpen sind zwar im Invest günstiger, aber bei den Betriebskosten deutlich schlechter als elektrisch betriebene Pumpen.
Quelle(n):
- Informationszentrum für betrieblichen Umweltschutz [IBU] (2012): Betrieblicher Umweltschutz [online]. Ministerium für Umwelt, Klima und Energiewirtschaft Baden-Württemberg, verfügbar unter: Link
Energieeinsparung bei Klimatisierung
Bei der Herstellung von Teilen mit sehr hohen Genauigkeitsanforderungen und in Messräumen erfordert der Prozess eine enge Temperaturspanne. Teilweise reicht es dabei nicht mehr aus, die einzelne Maschine zu temperieren. In diesen Fällen ist eine Klimatisierung des Raums erforderlich. Unter Berücksichtigung einiger Hinweise lässt sich der Energiebedarf in vielen Fällen senken:
- Temperatur möglichst nahe der üblichen Umgebungstemperatur einstellen. Oft nur aus Tradition oder Gewohnheit wird die Temperatur in klimatisierten Räumen bei 20 °C eingestellt. Erkundigen Sie sich bei Ihrem Gerätehersteller, ob z.B. Ihre Messeinrichtung auch auf 22 °C geeicht werden kann.
- Räume so weit wie möglich eingrenzen, z.B. durch Abhängen der Decke.
- Gute Isolierung nach außen, auch innerhalb des Gebäudes.
- Vermeiden Sie Wärmeeinträge; Geräte und Anlagen mit Abwärme nach außerhalb des klimatisierten Raumes verlagern. Rechner und Serverräume müssen heute nur noch eingeschränkt unter klimatisierten Bedingungen betrieben werden. Bei den heutigen Anlagen sind Raumtemperaturen von 25 °C kein Problem mehr. Wichtiger ist, dass die Rechner gut belüftet werden, so dass sich kein Wärmestau bilden kann. In Bereichen mit erhöhtem Staubanfall oder auch bei ölhaltiger Luft sollten die Schutzgitter der Lüfter von Zeit zu Zeit auf Verschmutzungen geprüft und ggf. gereinigt werden.
Quelle(n):
- Informationszentrum für betrieblichen Umweltschutz [IBU] (2012): Betrieblicher Umweltschutz [online]. Ministerium für Umwelt, Klima und Energiewirtschaft Baden-Württemberg, verfügbar unter: Link
Energieverbrauchsanalyse
- Eine Energieverbrauchsanalyse hilft, die Verbrauchsschwerpunkte im Unternehmen zu identifizieren.
- Die Einsparungspotenziale berechnen sich aus dem Ist-Zustand und dem, mit energieeffizienten Anlagen oder Techniken realisierbaren Energieverbrauch. Bei den in der Metallbranche typischen Schwerpunktsverbrauchern bestehen häufig große technische Einsparpotenziale beim Energieverbrauch, die bei Neuinvestitionen aber teilweise auch durch Nachrüstungen realisiert werden können.
- Der Energieverbrauch in metallverarbeitenden Betrieben setzt sich typischerweise aus dem Strombedarf (Maschinen, Anlagen, Beleuchtung usw.) und dem Energiebedarf zu Heizzwecken (Heizöl, Gas, evt. Solarenergie) zusammen. Bei der Heizenergie sollte noch zwischen der Raum- u. Gebäudeheizung und der Prozessheizenergie, die teilweise auch über Strom abgedeckt wird, unterschieden werden.
- Große Stromverbraucher sind beispielsweise Werkzeugmaschinen, die Versorgung mit Prozess- u. Hilfsstoffen (insb. Kühlschmierstoffen), Nebenanlagen wie Kompressoren, Klimageräte, Ventilatoren, Pumpen und die Beleuchtung.
- Große Wärmeverluste an Raumwärme entstehen bei der Zwangsentlüftung, offenen Hallentoren sowie bei Be- und Entladevorgängen. Ansatzpunkte für Energieeinsparungen bei der Gebäudeheizung gelten weitgehend brachenunabhängig für alle Betriebe.
Quelle(n):
- Informationszentrum für betrieblichen Umweltschutz [IBU] (2012): Betrieblicher Umweltschutz [online]. Ministerium für Umwelt, Klima und Energiewirtschaft Baden-Württemberg, verfügbar unter: Link
Instandhaltungs- und Serviceprozesse
- Effizienzsteigerung durch den Einsatz von Handhelds und Smartphones
- Fertigungsdaten direkt auf das mobile Endgerät: Entscheidungsgrundlagen in Echtzeit
Maßnahmen zur Abfallvermeidung beim Einsatz von nicht wassermischbaren Kühlschmierstoffen - KSS-Öle
- Bei den meisten Betrieben dürften erfahrungsgemäß die größten Potenziale bei Maßnahmen zur Reduzierung bzw. Rückführung der Austragsverluste und langfristig bei der Einführung der Trockenbearbeitung gegeben sein.
- Reduzierung der Austragsverluste: Die oft wesentlichste und effektivste indirekte Abfallvermeidungsmaßnahme ist bei KSS-Ölen die Reduzierung der Verschleppungen über Werkstücke, Späne, ggf. Schleifschlämme. Die ausgetragenen KSS-Mengen sind bei KSS-Ölen erheblich höher (bedingt durch die höhere Viskosität) als bei wassergemischten KSS und können ein Mehrfaches des Badinhalts pro Monat ausmachen. Diese gehen einerseits dem Arbeitsprozess verloren (Nachfüllbedarf, Kostenfaktor) und gelangen andererseits entweder in nachfolgende Prozesse (z. B. Waschbäder, reduziert deren Standzeit und bedeutet zusätzliche Abfallmenge) oder in die Entsorgung, oft zusammen mit Spänen oder Schlämmen.
Durch
-
- Abtropfzonen (Werkstücke, Späne)
- Schleudern (Kleinteile, Späne) sowie
- Auspressen oder Zentrifugieren (Späne, Schleifschlämme) lassen sich erhebliche Anteile der ausgetragenen KSS abtrennen. Diese können, ggf. über einen Feinfilter, umgehend in den KSS-Kreislauf zurückgeführt werden.
- Mengenminimierung beim KSS-Einsatz: Mit dem Grundsatz „so wenig wie möglich, so viel wie nötig“ lassen sich oft durch systematische Überprüfung des wirklich erforderlichen Bedarfs die KSS-Einsatzmengen deutlich reduzieren.
- Vereinheitlichung und Reduzierung der eingesetzten KSS-Sorten: Moderne KSS weisen heute ein breites Anwendungsspektrum auf, so dass die Anzahl der eingesetzten KSS auf ein Minimum reduziert werden kann. In den meisten Betrieben reichen 1–2 wassermischbare und 1–2 nicht wassermischbare KSS aus. Wenige KSS-Sorten vereinfachen die betriebliche Materialwirtschaft und Logistik und ermöglichen unter Umständen eine zentrale KSSVersorgung, was den Aufwand für Überwachung und Pflege reduziert und somit KSS-Mengen und Kosten einspart.
Quelle(n):
- Informationszentrum für betrieblichen Umweltschutz [IBU] (2012): Betrieblicher Umweltschutz [online]. Ministerium für Umwelt, Klima und Energiewirtschaft Baden-Württemberg, verfügbar unter: Link
Mechanische Ölnebelabscheider
- der Einsatz mechanischer Ölnebelabscheider führt zu geringeren Energie- und Wartungskosten
Minimalmengen-Schmierung (MMS)
- Unter Minimalmengen-Schmierung (MMS) versteht man das Aufbringen sehr geringer Schmierstoffmengen direkt auf den Wirkungsbereich Werkzeug/Werkstück.
- Mit MMS-Mengen (5 - 50ml/h) kann für die Trockenbearbeitung ein wesentlich breiterer Anwendungsbereich mit erhöhter Prozesssicherheit und deutlich verlängerten Werkzeugstandzeiten erschlossen werden. Die MMS ergänzt daher die Trockenbearbeitung um eine kostengünstige, betriebssichere und universell einsetzbare Technologie.
- Der Schmierstoffauftrag erfolgt meist mittels Sprühtechnik entweder von außen auf die Bearbeitungsstelle (äußere Zuführung) oder über die Werkzeugspindel durch das Werkzeug (z.B. bei Bohrern, Fräsern) über eingebrachte Kanäle zur Werkzeugschneide (innere Zuführung).
- Um die geringen Mengen im Bereich von 5 - 50 ml/h exakt und bedarfsgerecht dosiert auf die Wirkstelle aufzubringen, werden verschiedene Ausführungen der Sprühtechnik eingesetzt. Mit Luft als Träger- u. Führungsmedium (zur Reduzierung der Overspray-Verluste) werden feinste Schmierstofftröpfchen auf die Bearbeitungsstelle aufgebracht. Der Auftragstechnik kommt dabei eine wesentliche Bedeutung zu.
- MMS-Systeme sind in der Regel relativ kompakt und lassen sich auch bei bestehenden Werkzeugmaschinen gut nachrüsten. Bei äußerer Zuführung sollte die Düse dabei im Abstand von 3 - 15 cm auf den Eingriffsbereich des Werkzeugs gerichtet sein. Bei automatischen Werkzeugwechselsystemen ist auf die Kollisionsgefahr beim Werkzeugwechsel zu achten. Wegen des überschaubaren Investitionsaufwands (Gerätekosten: 1.000 - 6.000 EUR) und der einfachen Nachrüstmöglichkeit sind MMS-Anlagen gut für die Ausrüstung einzeln stehender Maschinen sowie im Werkstattbereich geeignet.
- Ein beispielhafter Kostenvergleich zeigt, dass die entscheidenden Kostenvorteile keineswegs aus der entfallenden Beschaffung und der Entsorgung der Kühlschmierstoffe (KSS) resultieren, sondern vielmehr aus den indirekten Kosten, wie z. B. Personal- u. Anlagenkosten zur Pflege, Überwachung und Maschinenreinigung. Je nach betrieblicher Situation können die mit dem MMS-Einsatz erzielbaren Vorteile sehr unterschiedlich ausfallen. Hier empfiehlt es sich, sich im Vorfeld einen Kostenüberblick über die eigenen mit dem KSS-Einsatz verbundenen Aufwendungen und Umweltrisiken zu verschaffen.
- Gegenüber der vollständigen Trockenbearbeitung ist die MMS mit zusätzlichen Kosten (Geräte und Schmiermittel). MMS sollte daher generell nur dann eingesetzt werden, wenn die Möglichkeiten der reinen Trockenbearbeitung vollständig ausgereizt sind (Werkzeug- u. Verfahrensoptimierung) und damit keine Prozesssicherheit erzielt werden konnte.
Quelle(n):
- Informationszentrum für betrieblichen Umweltschutz [IBU] (2012): Betrieblicher Umweltschutz [online]. Ministerium für Umwelt, Klima und Energiewirtschaft Baden-Württemberg, verfügbar unter: Link
Minimierung der KSS-Sorten
- Erfahrungen haben gezeigt, dass man in der Feinmechanik in der Regel mit 2 KSS-Sorten auskommt: Einer Emulsion und einem Öl.
- Vorteile: einfachere Beschaffung und Lagerung, geringere Verwechselungsgefahr, einfachere Überwachung und Pflege, kostengünstigere Entsorgung
- unterschiedliche Ansatzpunkte zur Abfall- u. Kostenreduzierung:
- KSS-Öle: Reduzierung und Rückführung der Austragsverluste über Späne und Produkte.
- KSS-Emulsionen: Verlängerung der Badstandzeiten durch verbesserte Randbedingungen, Wartung und Pflege.
- Der Verzicht auf Kühlschmierstoffe, d.h. die Trockenbearbeitung bzw. Minimalmengen-Schmierung ist im Bereich der Feinmechanik für viele Produktionsprozesse möglich, setzt aber dafür ausgelegte Werkzeugmaschinen voraus.
- Insbesondere bei Serienprozessen kann durch Trockenbearbeitung/MMS die Bearbeitungseffizienz gesteigert und Vorteile beim Umwelt- u. Arbeitsschutz erzielt werden. So kann z. B. häufig der komplette Reinigungsprozess entfallen.
Quelle(n):
- Informationszentrum für betrieblichen Umweltschutz [IBU] (2012): Betrieblicher Umweltschutz [online]. Ministerium für Umwelt, Klima und Energiewirtschaft Baden-Württemberg, verfügbar unter: Link
Mit dem KSS-Einsatz verbundenen Energiebedarf reduzieren
- Um die Kühlschmierstoffe gezielt an die Wirkstelle zu führen und im gebrauchsfähigen Zustand zu erhalten sind Pumpen und eine Kreislaufführung mit verschiedenen Stationen und Einrichtungen erforderlich. Wassergemischte KSS (Emulsionen und Lösungen ) sind diesbezüglich aufwendiger als nichtwassermischbare KSS (Öle). Verschiedene Untersuchungen in der Automobilindustrie haben gezeigt, dass der Energieverbrauch für die Kühlschmierstoffbereitstellung u. -aufbereitung bis zu 60 % des Stromverbrauchs eines Fertigungsprozesses ausmachen kann.
- Energieverbraucher bei KSS-Versorgungseinrichtungen sind insbesondere
- Pumpen: Zuführung zur Bearbeitungsstelle (teilweise werden hier Hochdruckpumpen mit bis zu 80 bar eingesetzt), Rückführung (falls Höhenunterschied nicht ausreichend, oft verbunden mit dem Abtransport der Späne, Schlämme)
- Filteranlagen und KSS-Pflegeeinrichtungen (z. B. Bandfilter, Skimmer, Zyklone, Zentrifugen)
- Absauganlagen und Ölnebelabscheider an den Bearbeitungsmaschinen
- Kühlsysteme (falls erforderlich: Luft, Wasser, Verdunster)
- KSS-Entsorgung, falls innerbetrieblich (Abwasserbehandlungsanlage, Emulsionsspaltanlage)
- Anlagen zur KSS-Abtrennung von Spänen und Werkstücken, z. B. Späneschleudern
- Nicht direkt, aber indirekt ist auch der Energieeinsatz von Entfettungs- u. Reinigungsanlagen mit in die Betrachtung einzubeziehen. Nicht mit Kühlschmierstoffen behaftete Teile können unter Umständen direkt weiterverarbeitet werden. Zumindest ist der Reinigungsaufwand deutlich geringer.
- Optimierungsmöglichkeiten bei einzelnen Komponenten:
- Häufig wird sehr großzügig mit KSS umgegangen. Da die Menge auch die erforderliche Pumpleistung bestimmt, sollten Sie die KSS-Menge generell auf das erforderliche Maß reduzieren. Installation einer bedarfsorientierten Leistungssteuerung der Versorgungspumpen: Da der KSS nie gleichmäßig über den gesamten Produktionszyklus benötigt wird, laufen die Pumpen sonst unnötig gegen den hydraulischen Widerstand, mit hohem Energiebedarf.
- Bei Ersatz und Neuinvestitionen: Elektromotore mit der höchsten Energieeffizienzklasse einsetzen.
- Effektive Pumpsysteme bedeuten auch einen geringeren Wärmeeintrag in den Kühlschmierstoff: Das entlastet das Kühlsystem.
Quelle(n):
- Informationszentrum für betrieblichen Umweltschutz [IBU] (2012): Betrieblicher Umweltschutz [online]. Ministerium für Umwelt, Klima und Energiewirtschaft Baden-Württemberg, verfügbar unter: Link
Nachverfolgbare Überwachung der Bearbeitungsabläufe
- RFID für sichere nachverfolgbare und reibungslose Betriebsabläufe (wenn die Maschine mit falschen Programmen oder Werkzeugen bestückt ist, kann dies den Fertigungsablauf erheblich behindern oder sogar die Spannvorrichtung zerstören)
- Qualitätsüberwachung
Optimierung des Energieverbrauchs
- automatisches Ausschalten von Anlagen und Maschinen
- effizienter Drucklufteinsatz
- Heizung: In den im Stahlbau üblichen Fertigungshallen haben sich Strahlungsheizungen bewährt.
- Absauganlagen sollten strömungsgünstig ausgelegt und nach Bedarf ansteuerbar sein. Bei langen Laufzeiten lohnen sich Lüftermotoren mit der höchsten Effizienzklasse.
Quelle(n):
- Informationszentrum für betrieblichen Umweltschutz [IBU] (2012): Betrieblicher Umweltschutz [online]. Ministerium für Umwelt, Klima und Energiewirtschaft Baden-Württemberg, verfügbar unter: Link
Papierlose Fertigungsmappen
- leichtere Aktualisierungen durch Einsatz von Tablets
- durch die bessere Aktualisierung kann ggf. Ausschuss gemindert bzw. die Produktivität gesteigert werden
- Papiereinsparung
Verbesserungspotenzial bei der Energieeffizienz
Ansatzpunkte mit Verbesserungspotenzial bei der Energieeffizienz bei Bearbeitungsmaschinen sind:
- Die Maschine sollte nur dann eingeschaltet werden, wenn sie auch wirklich genutzt wird.
- Einsatz der Nebenaggregate optimieren, z. B.
- wird beim Abschalten des Kühlschmierstoffs die Pumpe ausgeschaltet oder nur ein Ventil geschlossen? (die Pumpe läuft dann mit Höchstleistung gegen den hydraulischen Widerstand)
- ist die Maschinenraumabsaugung bedarfsgerecht ausgelegt (nicht überdimensioniert) und sind die Strömungswege frei (z. B. verschmutzte Spänegitter, Saugrohre)
- Falls ein Elektroantrieb ausgetauscht werden muss, fragen Sie Ihren Hersteller, ob auch ein Elektromotor der Effizienzklasse 1 eingebaut werden kann.
- Verfügen die (größeren) Antriebe über eine lastabhängige Steuerung? Wenn nein, dann prüfen Sie die Umrüstungsmöglichkeit.
- Auslegung von Motoren und Steuerungen auf die wirklich erforderliche Spindelleistung
- Reduzierung der Verluste von Führungen und Bettbahnen, Optimierung der Achsantriebe, Reduktion der bewegten Massen
- Einsatz reibungsminimierter und damit energieeffizienterer Lagerungen, z.B. durch Kugelrollenlager
- Reduzierung des Kühlschmierstoffbedarfs bzw. besser Auslegung der Maschine auf Trockenbearbeitung und Minimalmengenschmierung
- Reduzierung des Absaugvolumens aus dem Arbeitsraum, z. B. durch Optimierung der Erfassungsstelle und Minimierung des Arbeitsraums
- Reduzierung des Druckluftverbrauchs
- Optimierung des Hydrauliksystems hinsichtlich Umlaufmengen und Energieverbrauch der Systemkomponenten (z.B. Pumpen, Magnetventile)
Quelle(n):
- Informationszentrum für betrieblichen Umweltschutz [IBU] (2012): Betrieblicher Umweltschutz [online]. Ministerium für Umwelt, Klima und Energiewirtschaft Baden-Württemberg, verfügbar unter: Link
Verbesserungspotenzial bei der Energieeffizienz (Neuinvestitionen)
bei Neuinvestitionen ist die Einbeziehung des Energieverbrauchs bei der Investitionsentscheidung wichtig:
- Lassen Sie sich vom Hersteller den tatsächlichen Energiebedarf (nicht die Anschlussleistung) für die verschiedenen Betriebszustände angeben (Bearbeitung, Bereitschaft, Stand by) und vergleichen Sie damit über die Einsatzzeit (z.B. 5 Jahre) verschiedene Angebote unter Einbeziehung der Energiekosten.
- Überdimensionierte Antriebe sind uneffektiv! Bestimmen Sie die ausreichende Spindelleistung für die geplanten Bearbeitungsprozesse. Auf dieser Basis sollte vom Maschinenhersteller der notwendige Motor und der dazugehörige Steller ausgelegt werden.
- Prüfen Sie die Möglichkeit der Trockenbearbeitung oder Minimalmengenschmierung.
- Fragen Sie nach Optionen zur Reduzierung des Energiebedarfs (z.B. Einsatz von energieeffizienten Antrieben)
Quelle(n):
- Informationszentrum für betrieblichen Umweltschutz [IBU] (2012): Betrieblicher Umweltschutz [online]. Ministerium für Umwelt, Klima und Energiewirtschaft Baden-Württemberg, verfügbar unter: Link
Vereinfachung der Verfahrensabläufe durch Trockenbearbeitung
- auch bei kleineren Betrieben und im Werkstattbereich kann die Trockenbearbeitung/MMS sehr vorteilhaft eingesetzt werden, z.B. beim Sägen von Profilen, Stangen und Rohren: Vermeidung von an Stangenmaterialien entlanglaufende KSS und der Reinigung/Entfettung von Rohr- u. Profilmaterialien durch KSS-Verzicht
- Vorteile bei der Serienproduktion: durch Trockenbearbeitung/MMS kann eine Vereinfachung der Prozessabläufe möglich werden
- die in solchen Fällen realisierbaren Kosteneinsparungen übertreffen den Aufwand zur Erprobung und Einführung der Trockenbearbeitung bei Weitem
- Insbesondere neuere Entwicklungen bei den Werkzeugtechnologien (Beschichtungen, neue Werkstoffe, andere Geometrien) ermöglichen heute teilweise den gänzlichen (Trockenbearbeitung) oder zumindest teilweisen Verzicht auf Kühlschmierstoffe (Minimalmengen-Schmierung MMS).
- Insbesondere das Fräsen ist grundsätzlich sehr gut für die Trockenbearbeitung/MMS geeignet: Bei der Nassbearbeitung werden die Schneidplatten im unterbrochenen Schnitt durch den Kühlschmierstoff quasi einer Thermoschockbeanspruchung ausgesetzt. Dies ist bei Trockenbearbeitung/MMS nicht der Fall, so dass wesentlich höhere Standzeiten erzielt werden können. Wichtige Voraussetzung ist, dass das Gesamtsystem, insbesondere die Werkzeugmaschine, trockenbearbeitungsfähig ist oder entsprechend ausgerüstet werden kann.
- Insbesondere bei Neuinvestitionen sollten daher die Einsatzmöglichkeiten der Trockenbearbeitung geprüft werden
- Neben unbrauchbar gewordenen KSS resultieren noch weitere, im Wesentlichen KSS-bedingte Abfälle aus der spanenden Metallbearbeitung, z.B.:
- ölhaltige Schleif, Hon- u. Läppschlämme
- KSS-getränkte Filtermittel (Filtervliese, Filterpatronen)
- Ölbindemittel (aufsaugen verspritzter, verschütteter KSS)
- KSS-verunreinigte Putztücher und Arbeitskleidung
- verölte Späne (insbesondere beim Einsatz von KSS-Ölen)
- auch die Werkstücke sind beim Verlassen der Maschine mit KSS behaftet; dies lässt sich durch Abtropfen oder Schleudern reduzieren. Meistens müssen sie vor dem Weiterverarbeiten gereinigt werden, was wiederum Umweltbelastungen nach sich zieht.
Quelle(n):
- Informationszentrum für betrieblichen Umweltschutz [IBU] (2012): Betrieblicher Umweltschutz [online]. Ministerium für Umwelt, Klima und Energiewirtschaft Baden-Württemberg, verfügbar unter: Link
Umsetzungsbeispiele
Null Fehler durch integrierte Prozesskette vom CAD-System bis zur Fertigung
Die Ingersoll Werkzeuge GmbH fertigt zu 90 % Sonderwerkzeuge in sehr geringen Losgrößen (1 bis 3). Die Gefahr von Ausschüssen durch eine fehlerhafte Konfiguration der NC-Zerspanungsmaschinen ist bei dieser Art der Fertigung sehr hoch. Aus diesem Grund setzt das Unternehmen auf eine lückenlose Prozesskette vom CAD-System bis zur eigentlichen Fertigung, kombiniert mit einer Vorab-Simulation des Fertigungsvorgangs. Hierfür wird zusätzlich zur NC-Bahnplanung mit CAM ein Simulationstool eingesetzt, welches eine Kollisionsprüfung vereinfachen kann. Außerdem erfolgt hier automatisch ein Abgleich der Spezifikationen des gefertigten Bauteils mit dem CAD Modell. Um die Prozesskette mit möglichst wenig Aufwand realisieren zu können, wurden zusätzlich eigene Softwarelösungen entwickelt, die den NC-Programmierer dabei unterstützen, die benötigten Werkzeuge und Aufnahme auszuwählen und automatisch zusammenzubauen. Schnittstellen zwischen dem Simulationstool und dieser Eigenentwicklung erlauben darüber hinaus sogar, den Aufbau automatisch anzupassen, wenn im Simulationsmodell Kollisionen festgestellt wurden [Vogel Communications Group (2018)].
Quelle(n):
- Vogel Communications Group (2018): Auf Anhieb kollisionsfrei fertigen [online]. Vogel Communications Group, 07.09.18 [abgerufen am: 22. November 2018]. Link
Projekte
BMBF-Forschungsprojekte „Beat“
- In dem Forschungsprojekt "Bewertung der Energieeffizienz alternativer Prozesse und Technologieketten" (Beat) wurden Effizienzsteigerungen bei Zerspanungsprozessen untersucht.
- Im Mittelpunkt standen die Energieeffizienz alternativer zerspanender Technologieketten sowie komplexe Energie- und Stoffströme.
- Es wurde ein Softwaremodul geschaffen, mit dem Anwender ihre Produkte nach DIN EN ISO 14040/44 ökologisch bilanzieren und nach beliebigen Wirkungskategorien – wie z. B. CO₂-Äquivalenz und Primärenergiebedarf – auswerten können.
Demozelle Smarte Fabrik 4.0
- Simulation der Fertigung individueller Produkte in kleinen Stückzahlen durch "digitalen Zwilling" des Produktionsprozesses (digitale Prozesskette vom Produktmodell zum Produktionsprozess)
- Ermöglicht es, die Herstellbarkeit eines Produktes automatisch zu bewerten, den Prozess ggf. anzupassen und den Ressourcenverbrauch der Herstellung vorab abzuschätzen
- Demonstration dieser Vorgehensweise in der "Smart Factory 4.0" anhand eines vereinfachten Produktionsprozesses (Herstellung eines Kaffeeuntersetzers)
Effizientere Auslegung von Werkzeugmaschinen
- Ergebnis des Verbundprojekts "Energie MSP" war, dass vor allem der Aufbau des Spindelmotors und die Stromspeisung der Antriebe ein großes Potenzial, die Effizienz zu erhöhen, bieten. So könnten z. B. Komponentenhersteller durch Einsatz von Leichtbaumaterialien das Gewicht der Spindeln reduzieren. Dies spart nicht nur Energie beim Beschleunigen und Bremsen, sondern führt auch bei den Vorschubachsen zu einer höheren Energieeffizienz.
- Untersuchungen im Rahmen des "Ewotek"-Verbundprojekts zeigen, dass Kühlschmiermittel-Zufuhr und -aufbereitung, Hydrauliksystem, Kühlsystem und Asynchronmotor für den Spindelantrieb mehr als zwei Drittel des Gesamtenergieverbrauchs einer Werkzeugmaschine verursachen. Durch eine energieeffiziente Regelung und Nutzung dieser Aggregate könnten rund 30 % der bislang verbrauchten Energie eingespart werden.
EU-Projekt: eco2cut
- 33 Projektpartner aus Österreich, Deutschland und Belgien haben zwei Jahre lang am internationalen Kooperationsprojekt „eco2cut“ nach praxisnahen Lösungen gesucht, um den Ressourcenverbrauch in den Produktionsstätten zu optimieren.
- Der Schwerpunkt des Projektes liegt auf der energetischen Optimierung von Wertschöpfungsprozessen in Klein- und Mittelunternehmen.
Kühlschmierstoffe regenerativ gewinnen
- auf Tierfetten basierenden Kühlschmierstoffe als Alternative zu mineralöl- oder pflanzenölbasierte Schmierstoffen
Material- und Energieeffizienzpotenziale durch den Einsatz von Fertigungsdatenerfassung und -verarbeitung
Kurzanalyse: Beispiele aus der Praxis erläutern, wie durch den Einsatz von Fertigungsdatenerfassung und -verarbeitung in Unternehmen Material- und Energieeffizienz gesteigert werden können.
Zur kompletten ProjektbeschreibungMaximierung der Energieeffizienz von Werkzeugmaschinen (MAXIEM)
- Bei dem Ende 2012 abgeschlossenen Projekt Maxiem konnte den Energieverbrauch einer Demonstratormaschine um rund 50 % zu senken.
- Optimiert wurden beispielsweise Hydraulik und Druckluft, Schaltschrankklimatisierung, Maschinenkühlung, Kühlschmierung und Absaugung. Bezogen auf einen 3-Schicht-Betrieb mit sechs Arbeitstagen pro Woche (ohne Standby) konnte der Energieverbrauch von 101.547 auf 48.620 kWh/a reduziert werden.
Projekt NCplus: Energie verstärkt für die Zerspanung einsetzen
- Das Hauptziel des Projekts ‚NCplus‘ war, den Energieanteil zu erhöhen, der für die Arbeit unmittelbar am Werkstück aufgewendet wird, und gleichzeitig den Gesamtverbrauch um 30 % zu senken.
- Die im Projekt entwickelten Lösungen reichen von der Optimierung von Komponenten für die Kühlung und der Hydraulik-Anlage bis hin zur Entwicklung einer effizienten Frässpindel und einer spielfreien Haltebremse.
Projekt NCplus: Energie verstärkt für die Zerspanung einsetzen
- Das Hauptziel des Projekts ‚NCplus‘ war, den Energieanteil zu erhöhen, der für die Arbeit unmittelbar am Werkstück aufgewendet wird, und gleichzeitig den Gesamtverbrauch um 30 % zu senken.
- Die im Projekt entwickelten Lösungen reichen von der Optimierung von Komponenten für die Kühlung und der Hydraulik-Anlage bis hin zur Entwicklung einer effizienten Frässpindel und einer spielfreien Haltebremse.
Ressourcenmanagement – Managementsysteme und ihr Beitrag zur Steigerung der Ressourceneffizienz
Mit Managementsystemen lassen sich Prozesse systematisieren und dadurch effizienter gestalten. Daraus kann sich oftmals eine Reduzierung des Energieverbrauchs oder eine Steigerung der Produktqualität erreichen. Welche Vorteile ein Ressourcenmanagementsystem bietet, das die gängigen Managementsysteme vereint, zeigt die Kurzanalyse Nr. 13 des VDI Zentrums Ressourceneffizienz.
Zur kompletten ProjektbeschreibungÜberwachungs- und Regelungssysteme für Werkzeugmaschinen und Produktionsanlagen
- Ein kompaktes Gerät erfasst nahezu alle prozessrelevanten Energieformen und protokolliert die ermittelten Daten übersichtlich.
- So kann der Anwender die Energieströme in seiner Maschine erfassen und „stille Verbraucher“ identifizieren.
- Großes Einsparpotenzial, bietet erfahrungsgemäß die Maschinenperipherie, die aus Pumpen, Spanförderern und anderen Zusatzgeräten besteht, welche sehr einfach in den Ruhephasen abgeschaltet werden könnten.
VDMA-Initiative Blue Competence
- Stellschrauben für eine deutliche Energiedrosselung an Werkzeugmaschinen sind beispielsweise der Einsatz energieeffizienter Maschinenkomponenten, ein energiebewusster Maschineneinsatz durch Stand-by-Betrieb sowie die Steigerung der Produktivität.
- Kürzere Fertigungszeiten reduzieren den Energieverbrauch.
Vermeidung, Verminderung und Verwertung von gefährlichen Abfällen aus der Metallbe- und -verarbeitung
- Leitfaden für den Umgang mit ölhaltigen Schmierstoff und Schlamm bei der Entsorgen
- verschiedene technische und organisatorische Möglichkeiten
- Rangordnung „Vermeidung vor Verwertung vor Beseitigung“
Videos
Druckluft ganz leicht gemacht
Mit dem Aufruf des Videos erklären Sie sich einverstanden, dass Ihre Daten an YouTube übermittelt werden und dass Sie die Datenschutzerklärung gelesen haben.
LED-Leuchten sparen Energie
Mit dem Aufruf des Videos erklären Sie sich einverstanden, dass Ihre Daten an YouTube übermittelt werden und dass Sie die Datenschutzerklärung gelesen haben.
Rundgang LED-Technik in Unternehmen
Mit dem Aufruf des Videos erklären Sie sich einverstanden, dass Ihre Daten an YouTube übermittelt werden und dass Sie die Datenschutzerklärung gelesen haben.
Rundgang MSR Technologies
Mit dem Aufruf des Videos erklären Sie sich einverstanden, dass Ihre Daten an YouTube übermittelt werden und dass Sie die Datenschutzerklärung gelesen haben.
Schnell, genau und effizient mit Daten-Monitoring
Mit dem Aufruf des Videos erklären Sie sich einverstanden, dass Ihre Daten an YouTube übermittelt werden und dass Sie die Datenschutzerklärung gelesen haben.
Weniger Strom im Büro
Mit dem Aufruf des Videos erklären Sie sich einverstanden, dass Ihre Daten an YouTube übermittelt werden und dass Sie die Datenschutzerklärung gelesen haben.